Top drive control system
A control system and top drive technology, which is applied to the automatic control system of drilling, directional drilling, rotary drilling, etc., can solve the problem that the sliding drilling system cannot realize the switching of top drive control signals, and can not further eliminate the static friction of the drill string. Complicated issues
- Summary
- Abstract
- Description
- Claims
- Application Information
AI Technical Summary
Problems solved by technology
Method used
Image
Examples
Embodiment 1
[0037] As a preferred embodiment of the present invention, it discloses a top drive control system, which includes a top drive control man-machine interface, a top drive controller 2, a data conversion interface 3, and a forward and reverse control man-machine interface 4, which can Programmable controller 5, transfer switch 6, frequency converter 7, top drive 8, drill string 9 and position sensor 10, the man-machine interface for the top drive control is installed on the top drive controller 2, and the top drive controller 2 passes through The cable is connected to the transfer switch 6; the forward and reverse control man-machine interface 4 is connected to the programmable controller 5, and the programmable controller 5 is connected to the transfer switch 6 through a cable; the top drive controller 2 is connected to the programmable controller through the data conversion interface 3 The programming controller 5 is connected; the other end of the transfer switch 6 is connecte...
Embodiment 2
[0039] On the basis of Example 1, as another preferred embodiment of the present invention, as shown in the attached drawings, the present invention includes a top drive control man-machine interface, a top drive controller 2, a data conversion interface 3, front and back Turn control man-machine interface 4, programmable controller 5, transfer switch 6, frequency conversion governor 7, top drive 8, drill string 9 and position sensor 10.
[0040] In the case of compound drilling or sliding drilling without "support pressure", the operator inputs commands through the top drive control man-machine interface, and the top drive control man-machine interface converts the command into a specific data format through the internal microprocessor. The serial port, network card or USB port transmits the data to the top drive controller 2, and the top drive controller 2 calculates through the internal arithmetic unit to obtain the control signal to control the frequency converter 7, and th...
Embodiment 3
[0046] As the best embodiment of the present invention, on the basis of Embodiment 2, the top drive controller 2 adopted includes a central processing module 11, a power supply module 12, a data acquisition module 13, an instruction sending module 14, a power port 15, an input Port 16, output port 17, controller circuit board 18, top drive controller box 19. The central processing module 11 , the power supply module 12 , the data acquisition module 13 and the instruction sending module 14 are installed on the controller circuit main board 18 . The power port 15 , input port 16 and output port 17 are installed on the top drive controller box 19 .
[0047] The power supply port 15 is connected to the power supply module 12. Under normal operation, the power supply module 12 is charged by an external power supply connected to the power supply port 15, and at the same time drives the operation of the circuit elements in the entire control box. Start the emergency power supply and...
PUM
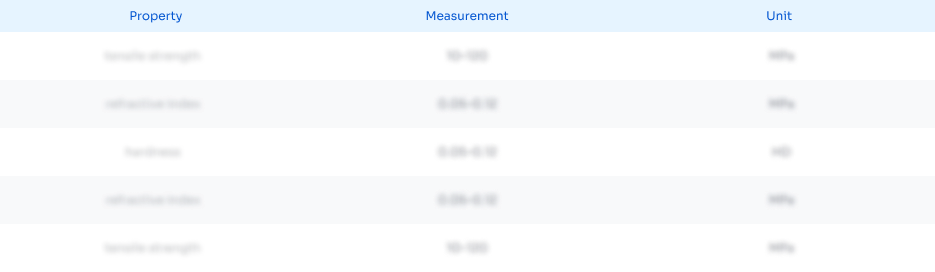
Abstract
Description
Claims
Application Information

- R&D
- Intellectual Property
- Life Sciences
- Materials
- Tech Scout
- Unparalleled Data Quality
- Higher Quality Content
- 60% Fewer Hallucinations
Browse by: Latest US Patents, China's latest patents, Technical Efficacy Thesaurus, Application Domain, Technology Topic, Popular Technical Reports.
© 2025 PatSnap. All rights reserved.Legal|Privacy policy|Modern Slavery Act Transparency Statement|Sitemap|About US| Contact US: help@patsnap.com