Low shrinkage mortar
A low-shrinkage, mortar technology, applied in the field of low-shrinkage mortar, can solve the problems of difficult to meet the rapid repair of the project, the wall decoration effect is deteriorated, the repair project duration is prolonged, etc., to achieve good thermal insulation effect, reduce shrinkage phenomenon, Guarantee the effect of quality of use
- Summary
- Abstract
- Description
- Claims
- Application Information
AI Technical Summary
Problems solved by technology
Method used
Examples
Embodiment 1
[0018] A low-shrinkage mortar, which contains 6.5% by mass of polytrimethylene carbonate modified kaolin and zeolite powder composite.
[0019] Further, the preparation method of polytrimethylene carbonate modified kaolin and zeolite powder composite includes the following steps: (1) kaolin pretreatment: mixing kaolin and catalyst into deionized water, stirring evenly, to obtain a mixed slurry , heated the mixed slurry to 86°C, then adjusted the pH of the mixed slurry to 8.6, then added 1.5% sodium bisulfite of the mixed slurry mass, continued heating to 90°C, stirred at 800r / min for 3 hours, and then filtered, using Wash with deionized water until neutral, dry to constant weight, and obtain pretreated kaolin;
[0020] (2) Zeolite powder pretreatment: add zeolite powder into the resistance furnace, calcinate at 750°C for 40min, then cool to 55°C, then add the cooled zeolite powder into hydrogen peroxide with a mass fraction of 30%, and stir for 10min Finally, add itaconic aci...
Embodiment 2
[0030] A low-shrinkage mortar, which contains 6.9% by mass of polytrimethylene carbonate modified kaolin and zeolite powder composite.
[0031] Further, the preparation method of polytrimethylene carbonate modified kaolin and zeolite powder composite includes the following steps: (1) kaolin pretreatment: mixing kaolin and catalyst into deionized water, stirring evenly, to obtain a mixed slurry , heated the mixed slurry to 86°C, then adjusted the pH of the mixed slurry to 8.6, then added 1.5% sodium bisulfite of the mixed slurry mass, continued heating to 90°C, stirred at 800r / min for 3 hours, and then filtered, using Wash with deionized water until neutral, dry to constant weight, and obtain pretreated kaolin;
[0032] (2) Zeolite powder pretreatment: add zeolite powder into the resistance furnace, calcinate at 750°C for 40min, then cool to 55°C, then add the cooled zeolite powder into hydrogen peroxide with a mass fraction of 30%, and stir for 10min Finally, add itaconic aci...
Embodiment 3
[0042] A kind of low-shrinkage mortar, containing 6.8% by mass of polytrimethylene carbonate modified kaolin and zeolite powder composite in the low-shrinkage mortar.
[0043]Further, the preparation method of polytrimethylene carbonate modified kaolin and zeolite powder composite includes the following steps: (1) kaolin pretreatment: mixing kaolin and catalyst into deionized water, stirring evenly, to obtain a mixed slurry , heated the mixed slurry to 86°C, then adjusted the pH of the mixed slurry to 8.6, then added 1.5% sodium bisulfite of the mixed slurry mass, continued heating to 90°C, stirred at 800r / min for 3 hours, and then filtered, using Wash with deionized water until neutral, dry to constant weight, and obtain pretreated kaolin;
[0044] (2) Zeolite powder pretreatment: add zeolite powder into the resistance furnace, calcinate at 750°C for 40min, then cool to 55°C, then add the cooled zeolite powder into hydrogen peroxide with a mass fraction of 30%, and stir for 1...
PUM
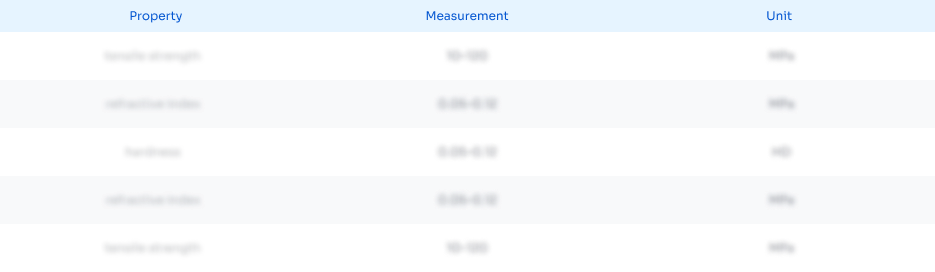
Abstract
Description
Claims
Application Information

- R&D
- Intellectual Property
- Life Sciences
- Materials
- Tech Scout
- Unparalleled Data Quality
- Higher Quality Content
- 60% Fewer Hallucinations
Browse by: Latest US Patents, China's latest patents, Technical Efficacy Thesaurus, Application Domain, Technology Topic, Popular Technical Reports.
© 2025 PatSnap. All rights reserved.Legal|Privacy policy|Modern Slavery Act Transparency Statement|Sitemap|About US| Contact US: help@patsnap.com