Method and system for digital extension of microscopic depth of field in microscopic vision system
A technology of microscopic vision and extension method, which is applied in the direction of instruments, measuring devices, and optical devices, etc., and can solve the problems of inability to observe, low precision, and technical difficulty of observation tasks, etc.
- Summary
- Abstract
- Description
- Claims
- Application Information
AI Technical Summary
Problems solved by technology
Method used
Image
Examples
Embodiment 1
[0063] figure 1 Shown is a microscopic depth of field extension system based on computerized microvisual tomography technology for a monocular microscopic vision system, which has a precise positioning system I (1) to control the microscopic vision system I (2) along the defined coordinate system (7) The Z-axis direction of the microscopic field of view is tomographically scanned, and the step size constraint of the precise positioning system for tomographically is as follows: figure 2 shown. according to figure 2 The schematic diagram of the relationship between the step length of the precision positioning system and the depth of field of the microscopic vision system shown in the figure, as shown in the label (14), the depth of the three-dimensional fault space of the microvision system that performs tomographic scanning along the Z axis is DOF, At this time, the three-dimensional space is H×W×DOF; if ΔDOF, as As shown in the label (15), the space size of the three-dime...
Embodiment 2
[0065] Figure 5 Shown is the depth of field extension system for the binocular orthogonal microscopic vision system, the hardware system structure of the depth of field extension of the binocular orthogonal microscopic vision system is as follows Figure 6 and Figure 7 shown; where Figure 7 The precision positioning system II (40) is added to control the microscopic vision system II (39) to perform tomographic scanning on the microscopic field of view space in the horizontal direction, and the precision positioning system I (1) controls the microscopic vision system I (2) to perform tomographic scanning in the vertical direction. Carry out tomographic scanning of the microscopic field of view space in the vertical direction. In order to realize the high-precision displacement monitoring of the precision positioning system (1, 40), displacement sensors are installed respectively to realize displacement detection such as Figure 6 As shown, the displacement sensors (31, 45...
Embodiment 3
[0067] Figure 8Shown is the depth of field extension system for the trinocular orthogonal microscopic vision system, in which the precision positioning system III (47) and the control microvision system III (48) are added, and the precision positioning system (1, 40, 47) is respectively Controlling the microscopic vision system (2, 39, 48) to perform tomographic scanning along the Z axis, X axis, and Y axis defining the coordinate system (7), and acquiring tomographic image sequences respectively. The trinocular orthogonal microscopic vision system is based on the computer microscopic vision tomography technology. The hardware system structure of the microscopic scene depth expansion is as follows: Figure 9 , Figure 10 shown. exist Figure 9 In the middle, the precise positioning system I (1) controls the microscopic vision system I (2) to perform tomographic scanning on the microscopic field of view space along the vertical direction, and the precise positioning system ...
PUM
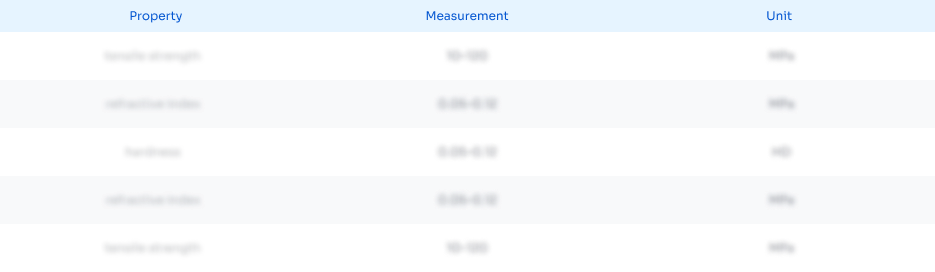
Abstract
Description
Claims
Application Information

- R&D Engineer
- R&D Manager
- IP Professional
- Industry Leading Data Capabilities
- Powerful AI technology
- Patent DNA Extraction
Browse by: Latest US Patents, China's latest patents, Technical Efficacy Thesaurus, Application Domain, Technology Topic, Popular Technical Reports.
© 2024 PatSnap. All rights reserved.Legal|Privacy policy|Modern Slavery Act Transparency Statement|Sitemap|About US| Contact US: help@patsnap.com