Vibration attenuation type magnetic levitation system track expansion adjusting structure
A telescopic adjustment and track technology, which is applied in the field of rail transit systems, can solve the problems of reducing the structural vibration of the maglev system track telescopic adjustment, and achieve the effects of improving track laying efficiency, avoiding functional failure, and reducing investment and operation and maintenance costs
- Summary
- Abstract
- Description
- Claims
- Application Information
AI Technical Summary
Problems solved by technology
Method used
Image
Examples
Embodiment Construction
[0021] The present invention will be further described below in conjunction with the accompanying drawings and embodiments.
[0022] refer to Figure 3 to Figure 7 , a kind of damping type magnetic levitation system rail telescopic adjustment structure of the present invention, comprises the rail row that is positioned on the bridge girder body 40, and described rail row is arranged on the bridge girder body 40 horizontally at least two rows of longitudinal guide grooves at intervals, and each row The longitudinal guide grooves are composed of longitudinally spaced longitudinal guide groove units 41 , and vertical limiting grooves 42 extending longitudinally are arranged on the two transverse side walls of each longitudinal guide groove unit 41 . Each longitudinal guide groove unit 41 is provided with elastic rollers 22 installed on the mounting base 21 through the telescopic shaft 23. Rows form a permanent connection. The rail row is supported on the elastic rollers 22, and...
PUM
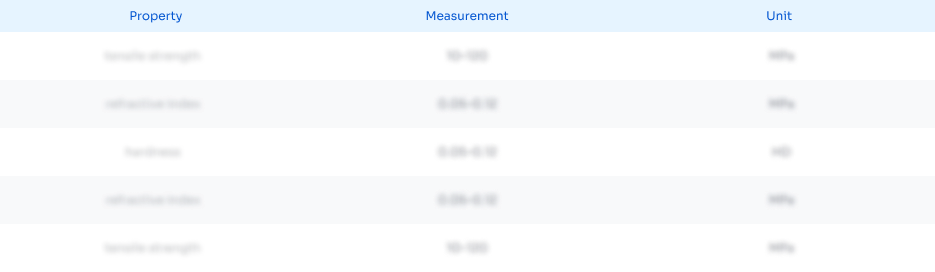
Abstract
Description
Claims
Application Information

- R&D Engineer
- R&D Manager
- IP Professional
- Industry Leading Data Capabilities
- Powerful AI technology
- Patent DNA Extraction
Browse by: Latest US Patents, China's latest patents, Technical Efficacy Thesaurus, Application Domain, Technology Topic, Popular Technical Reports.
© 2024 PatSnap. All rights reserved.Legal|Privacy policy|Modern Slavery Act Transparency Statement|Sitemap|About US| Contact US: help@patsnap.com