Environmentally-friendly flame-retardant floor leather and production method thereof
A production method and technology of floor leather, applied in the field of floor leather
- Summary
- Abstract
- Description
- Claims
- Application Information
AI Technical Summary
Problems solved by technology
Method used
Examples
Embodiment 1
[0022] An environment-friendly flame-retardant floor leather and a production method thereof. The floor leather sequentially includes a cloth base layer, a flame-retardant layer, and an anti-slip and wear-resistant layer. The raw materials of the flame-retardant layer and their mass percentages are: polyvinyl chloride 53.68%, phthalate di 26.13% capryl, 2.32% dioctyl sebacate, 4.12% methyl tin sulfate, 5.50% antimony trioxide, 3.19% zinc stearate, 3.78% acrylate copolymer, 1.28% mint, including the following production step:
[0023] (1) Add polyvinyl chloride, dioctyl phthalate, dioctyl sebacate, methyl tin sulfate, antimony trioxide, zinc stearate, acrylate copolymer and Mint, heat and stir, the heating temperature is 90-110°C, the stirring time is 10-15min, then cool the material to room temperature, and set aside;
[0024] (2) First heat the head of the extruder to 150-190°C, adjust the distance between the die lips to 2.0±0.2mm, wait until the body temperature reaches 17...
Embodiment 2
[0029] An environment-friendly flame-retardant floor leather and a production method thereof, wherein the floor leather sequentially includes a cloth base layer, a flame-retardant layer, and an anti-slip and wear-resistant layer. The raw materials and mass percentages of the flame-retardant layer are: polyvinyl chloride 48.13%, o Dioctyl phthalate 31.80%, dioctyl sebacate 2.20%, methyl tin sulfate 4.12%, aluminum hydroxide 5.50%, zinc stearate 3.19%, styrene copolymer 3.78%, licorice 1.28%, specific Including the following production steps:
[0030] (1) Add polyvinyl chloride, dioctyl phthalate, dioctyl sebacate, methyl tin sulfate, aluminum hydroxide, zinc stearate, styrene copolymer and licorice into the mixing chamber of the mixer in sequence , heating and stirring, the heating temperature is 90-110°C, the stirring time is 10-15min, and then the material is cooled to room temperature for use;
[0031] (2) First heat the head of the extruder to 150-190°C, adjust the distanc...
Embodiment 3
[0036] An environment-friendly flame-retardant floor leather and a production method thereof, wherein the floor leather sequentially comprises a cloth base layer, a flame-retardant layer and an anti-slip wear-resistant layer, and the raw materials and mass percentages of the flame-retardant layer are: polyvinyl chloride 49.47%, o Dioctyl phthalate 26.02%, Dioctyl sebacate 2.68%, Methyl tin sulfate 5.04%, Decabromodiphenylethane 6.72%, Molybdenum trioxide 3.89%, Styrene 4.62%, Grapefruit peel 1.56%, Specifically include the following production steps:
[0037] (1) Add polyvinyl chloride, dioctyl phthalate, dioctyl sebacate, methyl tin sulfate, decabromodiphenylethane, molybdenum trioxide, styrene and grapefruit into the mixing chamber of the mixer in sequence skin, heating and stirring, the heating temperature is 90-110°C, the stirring time is 10-15min, and then the material is cooled to room temperature and set aside;
[0038] (2) First heat the head of the extruder to 150-19...
PUM
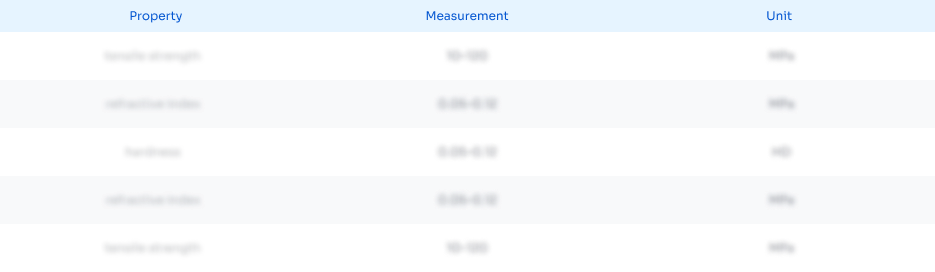
Abstract
Description
Claims
Application Information

- R&D
- Intellectual Property
- Life Sciences
- Materials
- Tech Scout
- Unparalleled Data Quality
- Higher Quality Content
- 60% Fewer Hallucinations
Browse by: Latest US Patents, China's latest patents, Technical Efficacy Thesaurus, Application Domain, Technology Topic, Popular Technical Reports.
© 2025 PatSnap. All rights reserved.Legal|Privacy policy|Modern Slavery Act Transparency Statement|Sitemap|About US| Contact US: help@patsnap.com