Production method of hotpot condiment packaging bag
A technology of hot pot bottom material and production method, which is applied in packaging, transportation and packaging, bag making operations, etc., and can solve the problems of low efficiency in making composite paper and easy peeling off of molten film
- Summary
- Abstract
- Description
- Claims
- Application Information
AI Technical Summary
Problems solved by technology
Method used
Image
Examples
Embodiment Construction
[0028] The following is further described in detail through specific implementation methods:
[0029] The reference signs in the accompanying drawings of the description include: unwinding roller 1, tackifying roller 2, corona roller 3, first driving roller 4, preheating roller 5, second driving roller 6, extrusion pair roller 7, third Drive roller 8, cooling roller 9, winding roller 10, preheating shell 11, cleaning roller 12, collecting box 13, scraper 14, filter cover 15, negative pressure blade 16, turbine shell 17, air outlet filter hole 18, air intake Hole 19, Extrusion Cylinder 20, Machine Head 21, Second Motor 22, Sector Spline Wheel 23, Spline Rod 24, Hopper 25, Feeding Pipe 26, First Wedge 27, Piston Cylinder 28, Extrusion Screw 29 , Cam 30, second wedge bar 31, third wedge bar 32, rack 33, support plate 34.
[0030] The embodiment is basically as attached figure 1 , figure 2 and image 3As shown: the production method of the hot pot bottom material packaging ba...
PUM
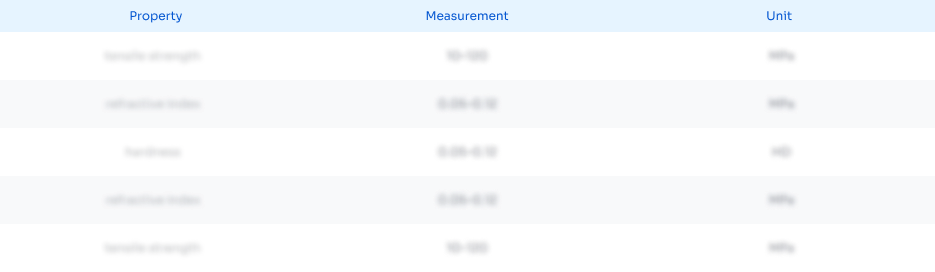
Abstract
Description
Claims
Application Information

- Generate Ideas
- Intellectual Property
- Life Sciences
- Materials
- Tech Scout
- Unparalleled Data Quality
- Higher Quality Content
- 60% Fewer Hallucinations
Browse by: Latest US Patents, China's latest patents, Technical Efficacy Thesaurus, Application Domain, Technology Topic, Popular Technical Reports.
© 2025 PatSnap. All rights reserved.Legal|Privacy policy|Modern Slavery Act Transparency Statement|Sitemap|About US| Contact US: help@patsnap.com