Motor car brake pipe end thermoforming device
A brake tube and thermoforming technology, applied in the direction of forming tools, manufacturing tools, metal processing equipment, etc., can solve the problems of inability to guarantee forging temperature, poor forming stability, increased manufacturing cycle and processing costs, etc., to achieve simple structure and improved Production efficiency and yield, and the effect of reducing manufacturing costs
- Summary
- Abstract
- Description
- Claims
- Application Information
AI Technical Summary
Problems solved by technology
Method used
Image
Examples
Embodiment Construction
[0017] Below the present invention will be further described in conjunction with the embodiment in the accompanying drawing:
[0018] Such as figure 1 As shown, the present invention mainly comprises an anvil 3, a die 5, a bulging brace 10 and a punch assembly. The front end of the bulging support 10 is a conical truncated part, and the rear end is a mandrel part. The mandrel part of the bulging supporting part 10 is fixed in the center of the bulging supporting part installation cavity. department. During processing, a brake pipe 6 is placed between the die 5 and the punch assembly, and the end face of the brake pipe 6 is pressed against the front end face of the anvil 3 .
[0019] The die 5 includes a die energizing part 5.1 and a die insulating part 5.2. The die energizing part 5.1 is arranged vertically, and the die insulating part 5.2 is arranged horizontally. Die energizing part 5.1 is in contact with brake tube 6. Die energizing part 5.1 is made of conductive materia...
PUM
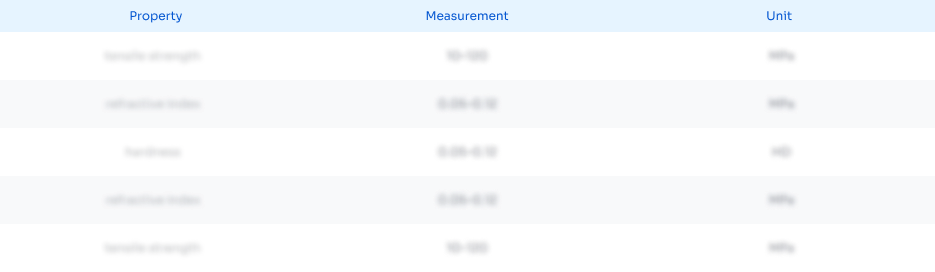
Abstract
Description
Claims
Application Information

- R&D Engineer
- R&D Manager
- IP Professional
- Industry Leading Data Capabilities
- Powerful AI technology
- Patent DNA Extraction
Browse by: Latest US Patents, China's latest patents, Technical Efficacy Thesaurus, Application Domain, Technology Topic, Popular Technical Reports.
© 2024 PatSnap. All rights reserved.Legal|Privacy policy|Modern Slavery Act Transparency Statement|Sitemap|About US| Contact US: help@patsnap.com