A reverse magnetic linear drive stepping motor
A linear drive and stepping motor technology, applied in electromechanical devices, electrical components, etc., can solve problems affecting the output accuracy of angular displacement, loss of distribution, high cost, etc., achieve low precision and assembly process requirements, simplify motor design, improve drop effect
- Summary
- Abstract
- Description
- Claims
- Application Information
AI Technical Summary
Problems solved by technology
Method used
Image
Examples
Embodiment 1
[0025] Such as figure 1 and figure 2 As shown, the present invention provides a reverse magnetic linear drive stepper motor, including a power unit 1 and a transmission unit 2 connected to the power unit 1, and the power unit 1 includes a reverse magnetic magnet 11 and is arranged on the reverse magnetic The coil group 12 on the periphery of the magnet 11, the transmission unit 2 includes a tooth row group 21 and a ratchet group 22 abutting against the tooth row group 21; the ratchet group 22 includes a ratchet 221 arranged on the upper part of the rotating shaft 211 and The ring gear 222 is disposed on the periphery of the ratchet 221 . The power unit 1 is used to generate power, and the transmission unit 2 is used to transmit the power of the power unit 1. During the power transmission process of the transmission unit 2, when the reverse magnetic linear drive step After the motor receives a pulse signal, the coil group 12 will generate a pulse movement along the circumfer...
Embodiment 2
[0030] Such as figure 1 and figure 2 As shown, as another preferred embodiment of the present invention, the reverse magnetic linear drive stepper motor further includes a rack 4 arranged between the power unit 1 and the transmission unit 2, and the reverse magnetic magnet The two ends of 11 are respectively connected with the inside of the rack 4; the rack 21 is U-shaped, the shaft 211 extends out of the rack 4, and the bottom of the shaft 211 is connected to the coil group 12 connected. The gear rack 4 facilitates the installation of the power unit 1 and the transmission unit 2, and protects the power unit 1, improving its safety performance.
[0031] A reset structure 3 is provided on the outer side of the rack 4, and the reset structure 3 is a reset spring or a reset elastic piece.
Embodiment 3
[0033] combine image 3 and Figure 4 As shown, as another preferred embodiment of the present invention, the gear rack 4 is in the shape of a quadrangular frame, the rotating shaft 211 protrudes from the gear rack 4, and the bottom of the rotating shaft 211 is connected to the coil group 12 . The gear rack 4 facilitates the installation of the power unit 1 and the transmission unit 2, and protects the power unit 1, improving its safety performance.
[0034] A reset structure is provided between the gear rack 4 and the coil winding block 13, and the reset structure is a reset spring or the reset elastic piece.
[0035] During the use of the reverse magnetic linear drive stepper motor of the present invention, when the PWM pulse signal directly drives the reverse magnetic magnet 11, the reverse magnetic magnet 11 and the coil group 12 will generate a pulse similar to the pulse signal. Compared with the traditional stepping motor, the response time is shorter, and the tooth r...
PUM
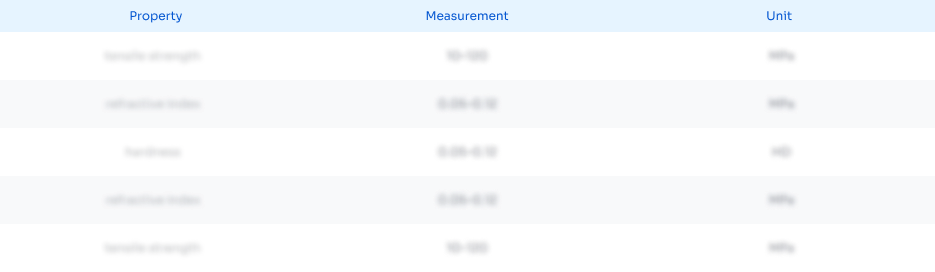
Abstract
Description
Claims
Application Information

- Generate Ideas
- Intellectual Property
- Life Sciences
- Materials
- Tech Scout
- Unparalleled Data Quality
- Higher Quality Content
- 60% Fewer Hallucinations
Browse by: Latest US Patents, China's latest patents, Technical Efficacy Thesaurus, Application Domain, Technology Topic, Popular Technical Reports.
© 2025 PatSnap. All rights reserved.Legal|Privacy policy|Modern Slavery Act Transparency Statement|Sitemap|About US| Contact US: help@patsnap.com