Flexible hinge micro-component bending test device with large range and high precision
A flexible hinge and bending test technology, which is applied in the direction of using a stable bending force to test the strength of materials, measuring devices, strength characteristics, etc., to meet the requirements of accurate detection, simple preparation process, and convenient experimental operation.
- Summary
- Abstract
- Description
- Claims
- Application Information
AI Technical Summary
Problems solved by technology
Method used
Image
Examples
Embodiment Construction
[0037] In order to make the purpose, technical solutions and advantages of the embodiments of the present invention clearer, the technical solutions in the embodiments of the present invention will be clearly and completely described below in conjunction with the embodiments of the present invention. Obviously, the described embodiments are part of the present invention Examples, not all examples. Based on the embodiments of the present invention, all other embodiments obtained by persons of ordinary skill in the art without creative efforts fall within the protection scope of the present invention.
[0038] Please refer to Figure 1 to Figure 9 , the flexible hinge micro-component bending test device with a large range and high precision in this embodiment is composed of a loading mechanism 1, a pressure sensing mechanism 2, a grating displacement sensing mechanism 3, a cutter head supporting mechanism 4 and a clamping mechanism 5;
[0039] The loading mechanism 1 is to outp...
PUM
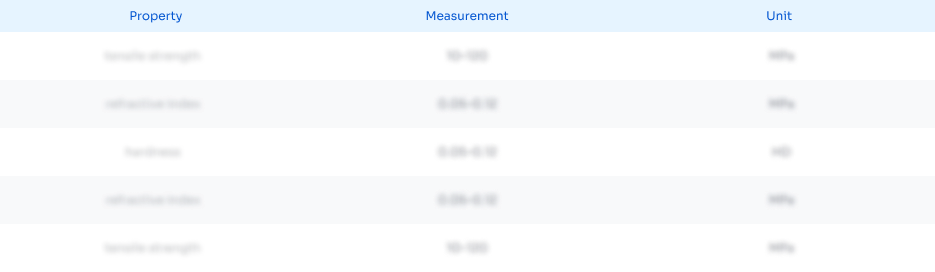
Abstract
Description
Claims
Application Information

- R&D Engineer
- R&D Manager
- IP Professional
- Industry Leading Data Capabilities
- Powerful AI technology
- Patent DNA Extraction
Browse by: Latest US Patents, China's latest patents, Technical Efficacy Thesaurus, Application Domain, Technology Topic, Popular Technical Reports.
© 2024 PatSnap. All rights reserved.Legal|Privacy policy|Modern Slavery Act Transparency Statement|Sitemap|About US| Contact US: help@patsnap.com