Resonant fatigue testing machine dynamic load error online compensation method
A technology of fatigue testing machine and dynamic load, which is applied in the field of error compensation, can solve problems such as poor compensation effect, and achieve the effect of improving measurement accuracy
- Summary
- Abstract
- Description
- Claims
- Application Information
AI Technical Summary
Problems solved by technology
Method used
Image
Examples
Embodiment Construction
[0034] The present invention will be further described below in conjunction with the figures.
[0035] refer to Figure 1 to Figure 7 , an online compensation method for a dynamic load error of a resonance type fatigue testing machine, comprising the following steps:
[0036] 1) Structural analysis of the vibration system of the resonant fatigue testing machine was carried out, the CT specimen connection model and the three-degree-of-freedom damped vibration dynamics model were established, and the dynamic equations were solved to obtain the displacement expressions of each mass of the vibration system. The theoretical expression of the dynamic load error on the fatigue testing machine is obtained by analyzing the real force value on the load cell, and the relevant factors affecting the dynamic load error are further analyzed;
[0037] 2) According to the actual working conditions of the resonance fatigue testing machine during the fatigue crack growth test, determine the key...
PUM
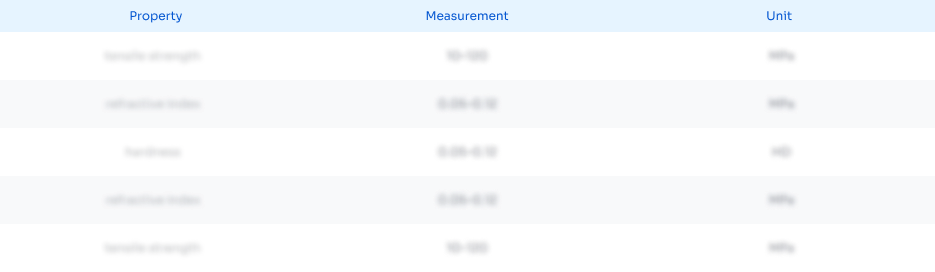
Abstract
Description
Claims
Application Information

- R&D
- Intellectual Property
- Life Sciences
- Materials
- Tech Scout
- Unparalleled Data Quality
- Higher Quality Content
- 60% Fewer Hallucinations
Browse by: Latest US Patents, China's latest patents, Technical Efficacy Thesaurus, Application Domain, Technology Topic, Popular Technical Reports.
© 2025 PatSnap. All rights reserved.Legal|Privacy policy|Modern Slavery Act Transparency Statement|Sitemap|About US| Contact US: help@patsnap.com