Copper rotor vacuum die-casting die
A vacuum die-casting and copper rotor technology, applied in the field of pure copper and copper alloy vacuum die-casting, induction motor copper rotor vacuum die-casting molds, can solve the problems of increased and difficult mold sealing design, and achieve increased exhaust capacity and vacuuming capacity, improving exhaust capacity and vacuuming effect, and solving the effect of insufficient vacuuming and exhausting capacity
- Summary
- Abstract
- Description
- Claims
- Application Information
AI Technical Summary
Problems solved by technology
Method used
Image
Examples
Embodiment Construction
[0029] The mold structure of the present invention will be described in detail below in conjunction with the accompanying drawings.
[0030] like figure 1The copper rotor vacuum die-casting mold shown includes a movable template 1, a static template 21 designed corresponding to the movable template 1, a core-pulling slider 14 installed on the movable template 1, and a movable mold insert set on the movable template 1 4 and the lower half block 2, the upper half block 11 installed on the core pulling slider 14, the static mold insert 25 and the pressure chamber 30 installed on the static template 20; the upper half block 11 and the lower half block 2 is provided with a dummy shaft 10, and an iron core 27 is stacked on the dummy shaft 10. One end of the iron core 27 is close to the movable mold insert 4, and the other end is set in the static mold after the movable template 1 and the static template 20 are closed. The static mold insert 25 on the template 20 fits closely; the m...
PUM
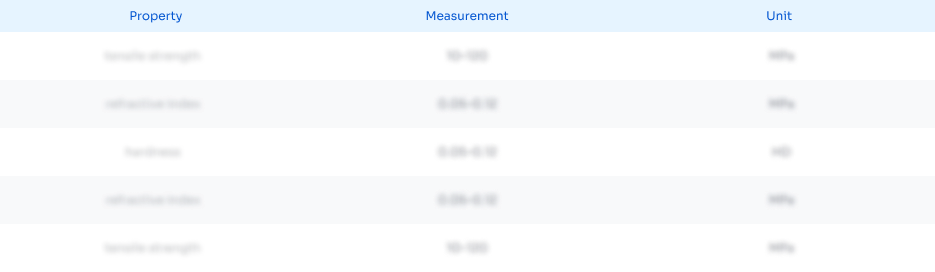
Abstract
Description
Claims
Application Information

- R&D Engineer
- R&D Manager
- IP Professional
- Industry Leading Data Capabilities
- Powerful AI technology
- Patent DNA Extraction
Browse by: Latest US Patents, China's latest patents, Technical Efficacy Thesaurus, Application Domain, Technology Topic, Popular Technical Reports.
© 2024 PatSnap. All rights reserved.Legal|Privacy policy|Modern Slavery Act Transparency Statement|Sitemap|About US| Contact US: help@patsnap.com