Fixed Constant Velocity Universal Coupling
A technology for universal couplings and couplings, which is applied in the direction of couplings, elastic couplings, and rotating parts that resist centrifugal force. Effect of less torque loss
- Summary
- Abstract
- Description
- Claims
- Application Information
AI Technical Summary
Problems solved by technology
Method used
Image
Examples
Embodiment Construction
[0034] Based on Figure 1~ Figure 10 One embodiment of the present invention will be described. Figure 1a It is a partial longitudinal sectional view of the fixed type constant velocity universal joint according to this embodiment, Figure 1b is the right side view. The constant velocity universal joint 1 is mainly composed of an outer joint member 2 , an inner joint member 3 , balls 4 and a cage 5 . Such as Figure 1b2 and 3, the respective eight raceway grooves 7, 9 of the outer coupling member 2 and the inner coupling member 3 are formed to be inclined in the circumferential direction with respect to the axis N-N of the coupling, and The inclination directions of the upwardly adjacent track grooves 7A, 7B and 9A, 9B are opposite to each other. Further, eight balls 4 are arranged at intersections of the paired track grooves 7A, 9A, 7B, 9B of the outer joint member 2 and the inner joint member 3 . exist Figure 1a Among them, regarding the raceway grooves 7 and 9, respec...
PUM
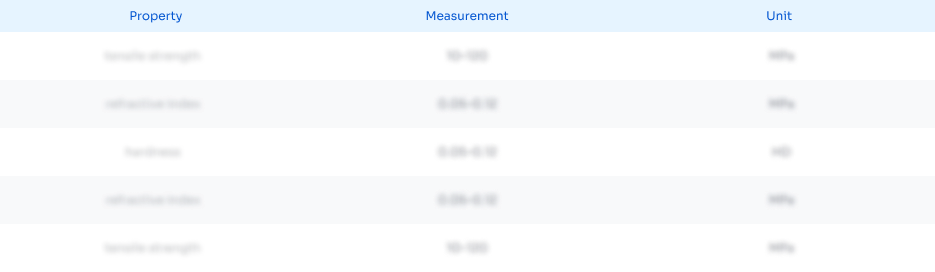
Abstract
Description
Claims
Application Information

- Generate Ideas
- Intellectual Property
- Life Sciences
- Materials
- Tech Scout
- Unparalleled Data Quality
- Higher Quality Content
- 60% Fewer Hallucinations
Browse by: Latest US Patents, China's latest patents, Technical Efficacy Thesaurus, Application Domain, Technology Topic, Popular Technical Reports.
© 2025 PatSnap. All rights reserved.Legal|Privacy policy|Modern Slavery Act Transparency Statement|Sitemap|About US| Contact US: help@patsnap.com