Preparation method of hydroxyapatite with controllable particle size
A hydroxyapatite, particle size technology, applied in chemical instruments and methods, phosphorus compounds, nanotechnology for materials and surface science, etc. Low dosage effect
- Summary
- Abstract
- Description
- Claims
- Application Information
AI Technical Summary
Problems solved by technology
Method used
Image
Examples
Embodiment 1
[0028] Dissolve 9.54g of calcium nitrate tetrahydrate and 3.20g of diammonium hydrogen phosphate in 100ml of deionized water, respectively. Weigh 0g, 0.02g, 0.1g, 0.2g and 0.6g (the numbers of the obtained products correspond to S1, S2, S3, S4 and S5 respectively) and add the hydrolyzed keratin into the calcium nitrate tetrahydrate solution. Under the condition of heating in a water bath at 95°C, slowly add the diammonium hydrogen phosphate solution into the mixed solution of calcium nitrate tetrahydrate and hydrolyzed keratin, while stirring and adding ammonia water to adjust the pH to 8.5. After reacting for 4 hours, heating and stirring were stopped, and the reaction system was allowed to stand and age for 12 hours, the precipitate was washed with water three times, and freeze-dried to obtain hydroxyapatite.
[0029] Figure 1 to Figure 5 The transmission electron micrographs of hydroxyapatite synthesized when the hydrolyzed keratin content (mass / solution volume) are respe...
Embodiment 2
[0033] Dissolve 95.4g of calcium nitrate tetrahydrate and 32.0g of diammonium hydrogen phosphate in 1000ml of deionized water respectively. Weigh 0g, 0.2g, 1g, 2g and 6g (the numbers of the obtained products correspond to S1, S2, S3, S4 and S5 respectively) and add the hydrolyzed keratin into the calcium nitrate tetrahydrate solution. Under the condition of heating in a water bath at 85°C, slowly add the diammonium hydrogen phosphate solution into the mixed solution of calcium nitrate tetrahydrate and hydrolyzed keratin, while stirring and adding ammonia water to adjust the pH to 12.5. After reacting for 5 hours, the heating and stirring were stopped, and the reaction system was left to age for 24 hours, the precipitate was washed 5 times with water, and dried at 110° C. for 5 hours to obtain the product hydroxyapatite.
[0034] Figure 8 It is the Raman characterization diagram of the hydroxyapatite prepared in Example 2. 425 and 580cm -1 The characteristic peaks at can be...
Embodiment 3
[0036] Dissolve 185.37g of calcium chloride and 380.14g of trisodium phosphate dodecahydrate in 1000ml of deionized water, respectively. Weigh 0g, 0.2g, 1g, 2g and 6g (corresponding to S1, S2, S3, S4 and S5 respectively) of hydrolyzed keratin and add it into the calcium nitrate tetrahydrate solution. Under the condition of heating in a water bath at 80°C, slowly add the diammonium hydrogen phosphate solution into the mixed solution of calcium nitrate tetrahydrate and hydrolyzed keratin, while stirring and adding ammonia water to adjust the pH to 11. After reacting for 5 hours, the heating and stirring were stopped, and the reaction system was aged for 24 hours. The precipitate was washed 5 times with water, and dried at 110° C. for 5 hours to obtain the product hydroxyapatite.
[0037] Figure 9 The hydroxyapatite polycrystalline X-ray diffraction characterization spectrum prepared in Example 3 shows that almost all peaks in the figure conform to the standard HA (JCPDS No. 0...
PUM
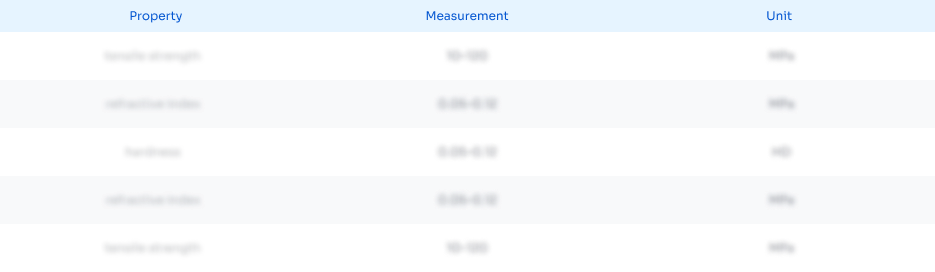
Abstract
Description
Claims
Application Information

- R&D Engineer
- R&D Manager
- IP Professional
- Industry Leading Data Capabilities
- Powerful AI technology
- Patent DNA Extraction
Browse by: Latest US Patents, China's latest patents, Technical Efficacy Thesaurus, Application Domain, Technology Topic, Popular Technical Reports.
© 2024 PatSnap. All rights reserved.Legal|Privacy policy|Modern Slavery Act Transparency Statement|Sitemap|About US| Contact US: help@patsnap.com