Equivalent method of predicting thermomechanical fatigue life
A thermomechanical fatigue and thermomechanical technology, applied in special data processing applications, instruments, electrical digital data processing, etc., can solve reliability uncertainty, ignore engine damage, etc.
- Summary
- Abstract
- Description
- Claims
- Application Information
AI Technical Summary
Problems solved by technology
Method used
Examples
Embodiment Construction
[0022] In order to make the objects and advantages of the present invention clearer, the present invention will be further described in detail below in conjunction with the examples. It should be understood that the specific embodiments described here are only used to explain the present invention, not to limit the present invention.
[0023] Embodiments of the present invention provide
[0024] An equivalent method for predicting thermomechanical fatigue life, comprising the following steps:
[0025] S1. According to the structural form of thermomechanics and the requirements of ride comfort and handling stability parameters, use ADAMS to establish a thermomechanical dynamic model, and obtain the ADAMS hard point file. The ADAMS hard point file at least includes the hard points of the thermomechanical location information;
[0026] S2, read the coordinate value of each hard point in the ADAMS hard point file, form a modifiable hard point table;
[0027] S3. Establish a har...
PUM
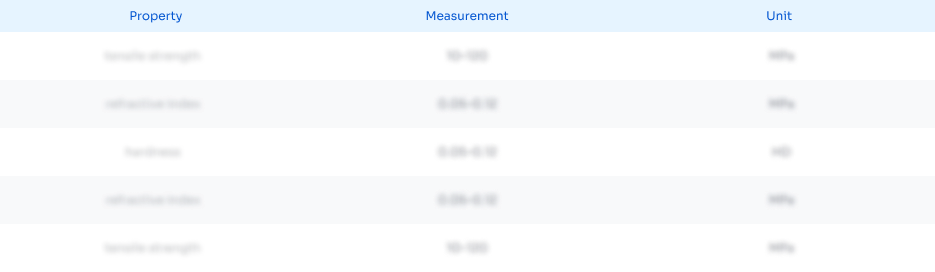
Abstract
Description
Claims
Application Information

- Generate Ideas
- Intellectual Property
- Life Sciences
- Materials
- Tech Scout
- Unparalleled Data Quality
- Higher Quality Content
- 60% Fewer Hallucinations
Browse by: Latest US Patents, China's latest patents, Technical Efficacy Thesaurus, Application Domain, Technology Topic, Popular Technical Reports.
© 2025 PatSnap. All rights reserved.Legal|Privacy policy|Modern Slavery Act Transparency Statement|Sitemap|About US| Contact US: help@patsnap.com