Train head model parameterization control method based on four-order partial differential equation
A technology of partial differential equation and control method, which is applied in the field of parameterized control of locomotive shape based on fourth-order partial differential equation, can solve the problem of taking a lot of time and storage space, unable to control the deflector, and unable to set out the local surface of the shape line. Adjustment of details and other issues to achieve the effect of multiple degrees of design freedom
- Summary
- Abstract
- Description
- Claims
- Application Information
AI Technical Summary
Problems solved by technology
Method used
Image
Examples
Embodiment
[0109] will be like figure 2 The traditional locomotive head model shown in a is discretized with a quadrilateral grid, and according to the symmetry of the train head shape, the following figure 2 Half of the quadrilateral gridded locomotive shape shown in b; in order to parametrically model the existing locomotive shape using partial differential equations, and realize the control of the shape of the locomotive shape; figure 2 The quadrilateral grid model shown in b is subdivided (in the present invention, half of the train head shape is divided into 17 patches, which are numbered as Patch1, Patch2...Patch17).
[0110] Pick figure 2 The quadrilateral mesh patch that has been divided in c, the patch number is Patch12, such as image 3 as shown in a; by image 3 a It can be seen that the shape of the patch is controlled by a large number of grid points, and if the method of finite difference is used to approximate all the grid points, the calculation efficiency will be ...
PUM
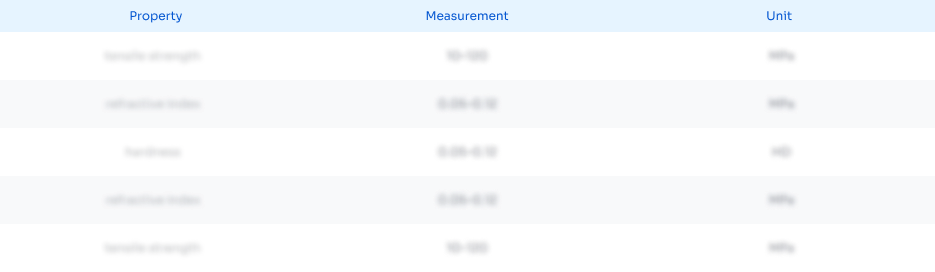
Abstract
Description
Claims
Application Information

- R&D
- Intellectual Property
- Life Sciences
- Materials
- Tech Scout
- Unparalleled Data Quality
- Higher Quality Content
- 60% Fewer Hallucinations
Browse by: Latest US Patents, China's latest patents, Technical Efficacy Thesaurus, Application Domain, Technology Topic, Popular Technical Reports.
© 2025 PatSnap. All rights reserved.Legal|Privacy policy|Modern Slavery Act Transparency Statement|Sitemap|About US| Contact US: help@patsnap.com