Traction wheel structure
A traction wheel and composite material layer technology, applied in the field of elevator traction wheels, can solve the problems of large wear, uneven wear, and increased cost of the traction rope, and achieve stable and reliable driving, high wear resistance, and lightening effect of weight
- Summary
- Abstract
- Description
- Claims
- Application Information
AI Technical Summary
Problems solved by technology
Method used
Image
Examples
Embodiment 1
[0033] Such as figure 1 As shown in (a-d), a single-layer composite material layer traction sheave structure includes:
[0034] The traction sheave connector 11 and the composite material layer 12, the composite material layer 12 is arranged on the outer circular working surface of the traction sheave body 11, and a traction sheave groove 13 is formed on the composite material layer 12; the traction sheave connector 11 has a shaft The hole 14 and the shaft hole 14 are provided with a spline groove 15 .
[0035] The composite material layer 12 is a single layer. The traction sheave connecting body 11 can be made of steel material, and the composite material layer 12 can be made of carbon fiber, or can be made of steel matrix composite carbon fiber through non-chemical treatment.
Embodiment 2
[0037] The only difference between this embodiment and Embodiment 1 is that: the traction sheave surface is formed on the composite material layer 12, and the traction sheave surface is formed by pressing the composite material layer 12 and then heat-treated. The traction belts work together to form a traction system. For other descriptions of the structure of the traction sheave, refer to the first embodiment above, which will not be repeated here.
[0038] In the traction sheave structure described in Embodiments 1 and 2, the existing traction groove or traction surface is directly set on the traction sheave connecting body, and an additional layer of composite material is added on the traction sheave connecting body, Set up a traction groove or traction surface on the composite material layer, which can reduce production costs, and can also choose to design the physical and mechanical properties such as the type, strength, and hardness of the composite material, and at the ...
Embodiment 3
[0040] Such as figure 2 As shown in (a-d), a traction sheave structure with double-layer composite material layers includes:
[0041] The traction wheel connector 21 and the composite material layer 22, the composite material layer 22 is arranged on the outer circular working surface of the traction wheel connector 21, the composite material layer 22 is a double layer, on the outer composite material layer of the composite material layer 22 A traction wheel groove 23 is formed; the traction wheel connecting body 21 has a shaft hole 24 , and a spline groove 25 is provided on the shaft hole 24 . The types of each layer of composite material layers can be the same or different, determined according to actual requirements. The traction sheave connecting body 21 can be made of steel material, and the double-layer composite material layer 22 can be made of carbon fiber and aramid fiber, and can also be made of metal matrix composite material and non-metallic composite material, an...
PUM
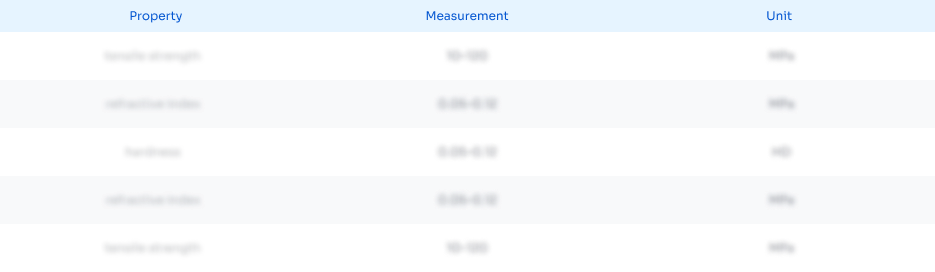
Abstract
Description
Claims
Application Information

- R&D
- Intellectual Property
- Life Sciences
- Materials
- Tech Scout
- Unparalleled Data Quality
- Higher Quality Content
- 60% Fewer Hallucinations
Browse by: Latest US Patents, China's latest patents, Technical Efficacy Thesaurus, Application Domain, Technology Topic, Popular Technical Reports.
© 2025 PatSnap. All rights reserved.Legal|Privacy policy|Modern Slavery Act Transparency Statement|Sitemap|About US| Contact US: help@patsnap.com