A rolling method of non-oriented high-grade silicon steel
A high-grade, silicon steel technology, applied in the field of cold-rolled strip rolling, can solve the problems of affecting the yield, high product hardness, and low production efficiency, reduce the number of broken strips and edge cracks, increase the rolling temperature, Effect of saving rolling time
- Summary
- Abstract
- Description
- Claims
- Application Information
AI Technical Summary
Problems solved by technology
Method used
Examples
Embodiment
[0029] Example: rolling 35AW230, 35AW210, 35AW270 (some operation methods of oriented silicon steel 30AG120 are still applicable)
[0030] The non-oriented high-grade silicon steel rolling method specifically includes the following steps:
[0031] 1) The first pass, the adjustment of the reduction rate of the rolling force: the preset rolling force is 4900kN, a large reduction rate of 39.2% is adopted, and the reduction rate is increased to increase the deformation temperature of the strip and increase the edge pressure of the strip Next, micro-edge wave rolling is adopted, that is, the pressure rate at the edge of the strip is slightly greater than the reduction rate at other positions of the strip. The rolling force mode (constant rolling force) is adopted when the machine is started to reduce the variation range of the strip shape, and the operator is given time to adjust the shape, so that the rolling is more stable and then switched to the position mode.
[0032] Adjustm...
PUM
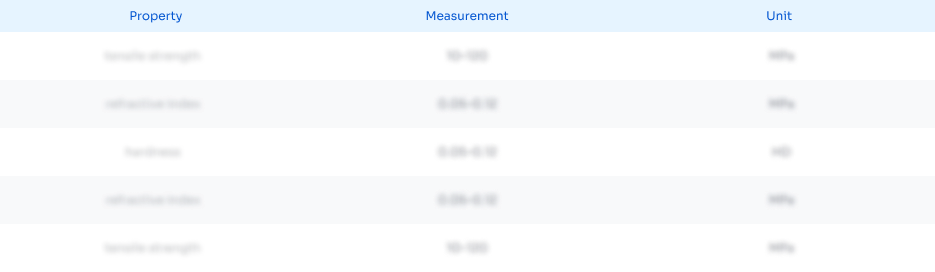
Abstract
Description
Claims
Application Information

- R&D
- Intellectual Property
- Life Sciences
- Materials
- Tech Scout
- Unparalleled Data Quality
- Higher Quality Content
- 60% Fewer Hallucinations
Browse by: Latest US Patents, China's latest patents, Technical Efficacy Thesaurus, Application Domain, Technology Topic, Popular Technical Reports.
© 2025 PatSnap. All rights reserved.Legal|Privacy policy|Modern Slavery Act Transparency Statement|Sitemap|About US| Contact US: help@patsnap.com