A method of preparing oxide film on the surface of magnesium alloy by micro-arc oxidation
A technology of micro-arc oxidation and magnesium alloy, applied in the direction of anodic oxidation, surface reaction electrolytic coating, coating, etc., can solve the problem of closed internal gas escape channel, phosphate human body and environmental hazards, film formation speed and poor corrosion resistance To achieve the effect of suppressing tip discharge, stabilizing the micro-arc oxidation process, and reducing pores
- Summary
- Abstract
- Description
- Claims
- Application Information
AI Technical Summary
Problems solved by technology
Method used
Image
Examples
Embodiment 1
[0027] Clean the magnesium alloy with alkaline solution to remove its surface oil, and then clean it with water. The magnesium alloy is placed in the electrolytic cell, and the electrolyte composition in the electrolytic cell is NaOH 10g / L, NaOH 2 SiO 3 15g / L, KF 6g / L, H 2 o 2(30%) 3mL / L, glycerin 6mL / L, sodium ethylenediamine tetramethylene phosphonate 2g / L, and the balance is water. A pulse power supply with a frequency of 400 Hz and a duty cycle of 15% is used to apply voltage to the electrolytic anode and cathode to cause plasma discharge on the magnesium alloy. The arc oxidation method forms an oxide film on the surface of the magnesium alloy.
Embodiment 2
[0029] Clean the magnesium alloy with alkaline solution to remove its surface oil, and then clean it with water. The magnesium alloy is placed in the electrolytic cell, and the electrolyte composition in the electrolytic cell is NaOH 10g / L, NaOH 2 SiO 3 15g / L, KF 6g / L, H 2 o 2 (30%) 3mL / L, glycerin 6mL / L, sodium ethylenediamine tetramethylene phosphonate 2g / L, and the balance is water. A pulse power supply with a frequency of 400 Hz and a duty cycle of 15% is used to apply voltage to the electrolytic anode and electrolytic cathode to cause plasma discharge on the magnesium alloy. During the process, the temperature in the electrolytic tank is controlled at 35°C. Add zeolite powder into the liquid, continue to react for 10 minutes, then add gamma-alumina nanometer powder to the electrolytic solution, continue to react for 10 minutes to form an oxide film on the surface of the magnesium alloy. The amount of zeolite powder added is 0.5% of the weight of the electrolyte, and ...
Embodiment 3
[0031] Clean the magnesium alloy with alkaline solution to remove its surface oil, and then clean it with water. The magnesium alloy is placed in the electrolytic cell, and the electrolyte composition in the electrolytic cell is NaOH 10g / L, NaOH 2 SiO 3 15g / L, KF 6g / L, H 2 o 2 (30%) 3mL / L, glycerin 6mL / L, sodium ethylenediamine tetramethylene phosphonate 2g / L, and the balance is water. A pulse power supply with a frequency of 400 Hz and a duty cycle of 15% is used to apply voltage to the electrolytic anode and electrolytic cathode to cause plasma discharge on the magnesium alloy. During the process, the temperature in the electrolytic tank is controlled at 35°C. Add zeolite powder into the liquid, continue to react for 10 minutes, then add gamma-alumina nanometer powder to the electrolytic solution, continue to react for 10 minutes to form an oxide film on the surface of the magnesium alloy. The amount of zeolite powder added is 0.5% of the weight of the electrolyte, and ...
PUM
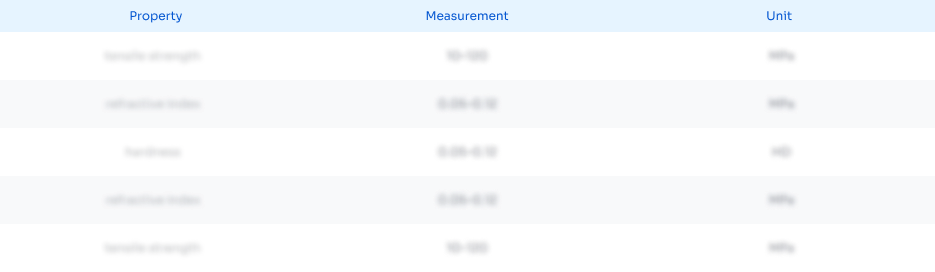
Abstract
Description
Claims
Application Information

- Generate Ideas
- Intellectual Property
- Life Sciences
- Materials
- Tech Scout
- Unparalleled Data Quality
- Higher Quality Content
- 60% Fewer Hallucinations
Browse by: Latest US Patents, China's latest patents, Technical Efficacy Thesaurus, Application Domain, Technology Topic, Popular Technical Reports.
© 2025 PatSnap. All rights reserved.Legal|Privacy policy|Modern Slavery Act Transparency Statement|Sitemap|About US| Contact US: help@patsnap.com