Preparation method of new fluorine-containing composite board material
A new material and composite technology, applied in the direction of chemical instruments and methods, laminated, layered products, etc., can solve the problems of limited application range, mechanical strength difference of protein plastics, etc., achieve wide application prospects, improve and mechanical properties, The effect of improving mechanical properties
- Summary
- Abstract
- Description
- Claims
- Application Information
AI Technical Summary
Problems solved by technology
Method used
Image
Examples
Embodiment 1
[0018] A preparation method for a new fluorine-containing composite board material, the preparation technical scheme is as follows:
[0019] According to the number of parts by mass, weigh 8 parts of urea and 170 parts of deionized water and add them to the reaction kettle. After stirring and completely dissolving, put 95 parts of protein powder into the reaction kettle, control the reaction temperature at 35°C, and react for 3 hours. Use sodium hydroxide solution to adjust the pH of the system to 11, then heat to 60°C, and react for 40 minutes; after the reaction is completed, add 0.3 parts of dispersant sodium tripolyphosphate, 8 parts of plasticizer, and 2 parts of polyacrylamide Benzylidene camphor, 8 parts zinc cocoeth sulfate, 0.3 parts by weight PEG-8 / trifluoropropyl dimethicone copolymer, 0.03 parts of stearyl hydroxyethyl imidazoline Nitrogenium chloride, 32 parts of cross-linking agent and 13 parts of modified nano-filler, continue to stir at high speed for 90 minute...
Embodiment 2
[0027] A preparation method for a new fluorine-containing composite board material, the preparation technical scheme is as follows:
[0028] According to the number of parts by mass, weigh 6 parts of urea and 150 parts of deionized water and add them to the reaction kettle. After stirring and completely dissolving, put 90 parts of protein powder into the reaction kettle, control the reaction temperature at 30°C, and react for 1 hour. Use sodium hydroxide solution to adjust the pH of the system to 10, then heat to 50°C, and react for 30 minutes; after the reaction is completed, add 0.5 parts of dispersant sodium tripolyphosphate, 5 parts of plasticizer, and 1 part of polyacrylamide Benzylidene camphor, 5 parts zinc cocoeth sulfate, 0.1 parts by weight PEG-8 / trifluoropropyl dimethicone copolymer, 0.01 parts of stearyl hydroxyethyl imidazoline Nitrogenium chloride, 25 parts of cross-linking agent and 10 parts of modified nano filler, continue to stir at high speed for 60 minutes,...
Embodiment 3
[0036] A preparation method for a new fluorine-containing composite board material, the preparation technical scheme is as follows:
[0037] According to the number of parts by mass, weigh 10 parts of urea and 180 parts of deionized water and add them to the reaction kettle. After stirring and completely dissolving, put 100 parts of protein powder into the reaction kettle, control the reaction temperature at 40°C, and react for 5 hours. Use sodium hydroxide solution to adjust the pH of the system to 12, then heat to 50-70°C, and react for 50 minutes; after the reaction is completed, add 0.5 parts of dispersant sodium tripolyphosphate, 10 parts of plasticizer, and 5 parts of polypropylene Amidomethylbenzylidene Camphor, 15 parts Zinc Cocoeth Sulfate, 0.5 parts by weight PEG-8 / Trifluoropropyl Dimethicone Copolymer, 0.06 parts of Stearyl Hydroxyethyl Imidazolinium chloride, 40 parts of cross-linking agent and 10-15 parts of modified nano-filler, continue to stir at high speed for...
PUM
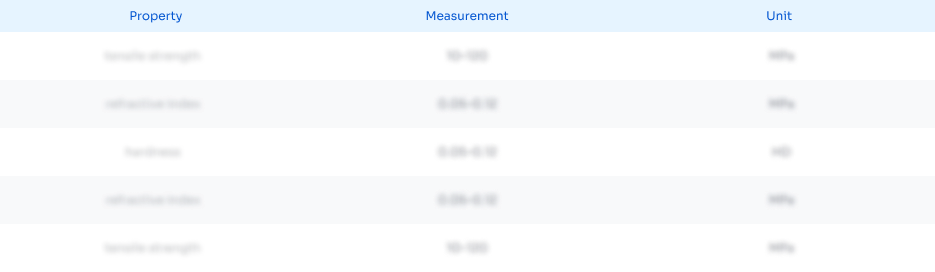
Abstract
Description
Claims
Application Information

- Generate Ideas
- Intellectual Property
- Life Sciences
- Materials
- Tech Scout
- Unparalleled Data Quality
- Higher Quality Content
- 60% Fewer Hallucinations
Browse by: Latest US Patents, China's latest patents, Technical Efficacy Thesaurus, Application Domain, Technology Topic, Popular Technical Reports.
© 2025 PatSnap. All rights reserved.Legal|Privacy policy|Modern Slavery Act Transparency Statement|Sitemap|About US| Contact US: help@patsnap.com