Milling three-dimensional stability forecasting method of six-freedom-degree series robot
A technology of stability prediction and milling processing, applied in the directions of manipulators, manufacturing tools, program-controlled manipulators, etc., it can solve problems such as obstacles in the application of criteria, inaccurate identification, and inability to accurately obtain included angles, so as to avoid modal coupling flutter. , The effect of improving the quality of the machined surface
- Summary
- Abstract
- Description
- Claims
- Application Information
AI Technical Summary
Problems solved by technology
Method used
Image
Examples
Embodiment Construction
[0045] The specific implementation manners of the present invention will be further described in detail below in conjunction with the accompanying drawings and embodiments. The following examples are used to illustrate the present invention, but are not intended to limit the scope of the present invention.
[0046] A three-dimensional stability prediction method for six-degree-of-freedom tandem robot milling, such as figure 1 shown, including the following steps:
[0047] Step 1: Determine the processing pose of the six-degree-of-freedom serial robot, and obtain the angle value of each joint of the six-degree-of-freedom serial robot.
[0048] In this embodiment, the workpiece fixture is installed first, the six-degree-of-freedom serial robot is manipulated to the processing pose, and the six joint angle values of the six-degree-of-freedom serial robot are recorded to ensure that the milling cutter is perpendicular to the workpiece surface for orthogonal cutting.
[0049] S...
PUM
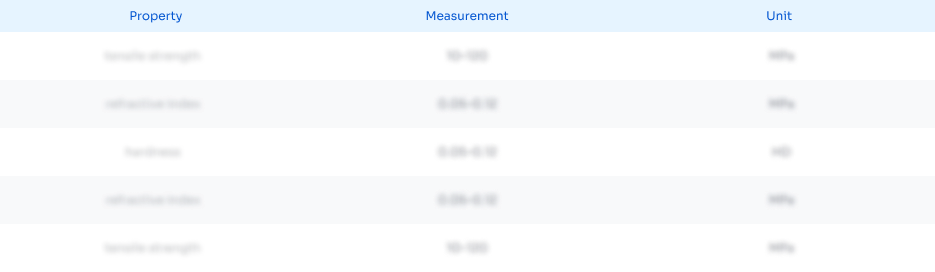
Abstract
Description
Claims
Application Information

- Generate Ideas
- Intellectual Property
- Life Sciences
- Materials
- Tech Scout
- Unparalleled Data Quality
- Higher Quality Content
- 60% Fewer Hallucinations
Browse by: Latest US Patents, China's latest patents, Technical Efficacy Thesaurus, Application Domain, Technology Topic, Popular Technical Reports.
© 2025 PatSnap. All rights reserved.Legal|Privacy policy|Modern Slavery Act Transparency Statement|Sitemap|About US| Contact US: help@patsnap.com