Waterproof thermal insulation coating
A technology of thermal insulation coating and expanded perlite, which is used in antifouling/underwater coatings, anticorrosive coatings, fireproof coatings, etc. The effect needs to be improved to achieve the effect of low brush thickness requirement, good stain resistance and good core-shell coating
- Summary
- Abstract
- Description
- Claims
- Application Information
AI Technical Summary
Problems solved by technology
Method used
Image
Examples
Embodiment 1
[0029] The preparation method of modified expanded perlite is:
[0030] Add expanded perlite to water containing 2wt% sodium lauryl sulfate, then add dropwise 150g / L indium trichloride solution and 100g / L tin tetrachloride solution, stir evenly, add 30% urea, and ultrasonically disperse Then gradually raise the temperature to 85°C for precipitation, wash with water after the precipitation, then raise the temperature to 500°C at 20°C / h, keep it for 50 minutes, then raise the temperature to 1000°C at 100°C / h, keep it for 3 hours, and you can get the modified Expanded perlite.
[0031] Acrylic emulsion, calculated in parts by weight, includes the following raw materials:
[0032] 170 parts of hydroxymethyl methacrylate, 90 parts of styrene, 15 parts of ammonium acrylate, 80 parts of alkaline silica sol, 46 parts of isooctyl acrylate, 105 parts of α-ethylhexyl acrylate, 20 parts of hydroxyethyl acrylate, 430 parts of water, 2 parts of potassium persulfate, 3.4 parts of pH regula...
Embodiment 2
[0040] The preparation method of modified expanded perlite is:
[0041] Add expanded perlite to water containing 1wt% sodium stearate, then add dropwise 100g / L indium trichloride solution and 150g / L tin tetrachloride solution, stir evenly, add 30% urea, and gradually Raise the temperature to 65°C for precipitation, wash with water after the precipitation, then raise the temperature to 700°C at 30°C / h, keep it for 30 minutes, then raise the temperature to 900°C at 80°C / h, keep it for 5 hours, and you can get the modified expanded pearl rock.
[0042] Acrylic emulsion, calculated in parts by weight, includes the following raw materials:
[0043] 180 parts of hydroxymethyl methacrylate, 100 parts of styrene, 13 parts of ammonium acrylate, 95 parts of non-ionic silica sol, 40 parts of isooctyl acrylate, 110 parts of α-ethylhexyl acrylate, 25 parts of hydroxyethyl acrylate , 460 parts of water, 2.5 parts of ammonium persulfate, 4 parts of pH regulator and 6 parts of sodium dodecy...
Embodiment 3
[0051] A waterproof and heat-insulating coating, calculated by weight percentage, comprising the following components:
[0052] 90 parts of alkyd resin, 50 parts of acrylic emulsion of Example 1, 26 parts of modified expanded perlite of Example 1, 10 parts of polyacrylic acid sodium salt, 6 parts of wetting agent, 12 parts of diethylenetriamine, thickener 6 parts and 20 parts of water. The thickener is a mixture of diatomaceous earth, sodium bentonite and microcrystalline cellulose.
PUM
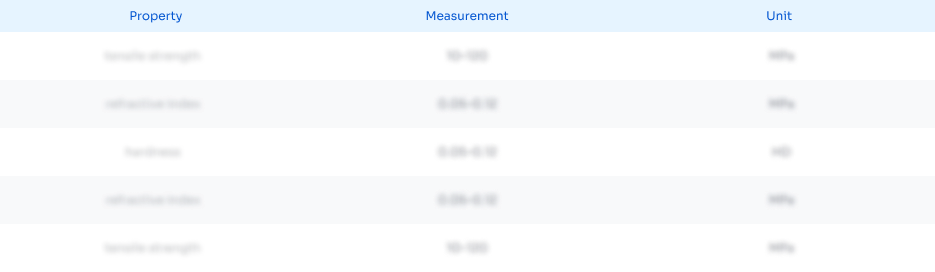
Abstract
Description
Claims
Application Information

- R&D
- Intellectual Property
- Life Sciences
- Materials
- Tech Scout
- Unparalleled Data Quality
- Higher Quality Content
- 60% Fewer Hallucinations
Browse by: Latest US Patents, China's latest patents, Technical Efficacy Thesaurus, Application Domain, Technology Topic, Popular Technical Reports.
© 2025 PatSnap. All rights reserved.Legal|Privacy policy|Modern Slavery Act Transparency Statement|Sitemap|About US| Contact US: help@patsnap.com