Tightening clamp for hinge screw tightening robot
A technology of robots and tightening tools, applied in the direction of chucks, manipulators, manufacturing tools, etc., can solve problems such as small torque, and achieve the effect of compact structure and high reliability
- Summary
- Abstract
- Description
- Claims
- Application Information
AI Technical Summary
Problems solved by technology
Method used
Image
Examples
Embodiment Construction
[0023] The present invention will be described in further detail below in conjunction with the accompanying drawings and specific embodiments, and the implementation scope of the present invention is not limited thereto.
[0024] Such as Figure 2 to Figure 8 As shown, the tightening jig for a hinge screw tightening robot described in this embodiment includes a top cap 1, and one end of the top cap 1 is provided with a round hole 13, and the round hole 13 extends into the top cap 1 forming a cavity 131;
[0025] Also includes a central shaft 3 and a first spring 6, one end of the central shaft 3 extends into the cavity 131, the other end of the central shaft 3 is provided with a push rod 32 and a bracket 31, and the bracket 31 includes three A group of U-shaped blocks 311 whose openings are facing away from the central axis 3, the bottoms of the three groups of U-shaped blocks 311 are connected in the same horizontal plane, and the bottoms of the three groups of U-shaped bloc...
PUM
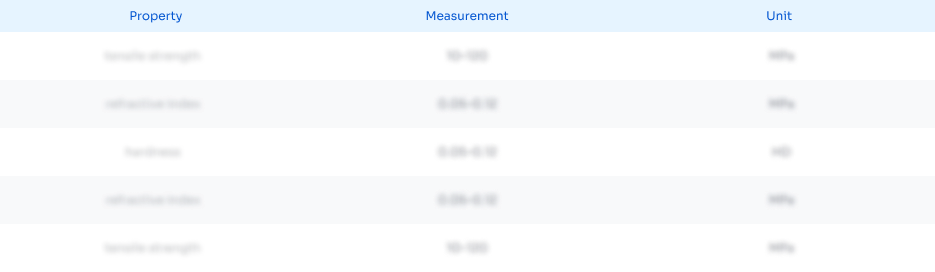
Abstract
Description
Claims
Application Information

- Generate Ideas
- Intellectual Property
- Life Sciences
- Materials
- Tech Scout
- Unparalleled Data Quality
- Higher Quality Content
- 60% Fewer Hallucinations
Browse by: Latest US Patents, China's latest patents, Technical Efficacy Thesaurus, Application Domain, Technology Topic, Popular Technical Reports.
© 2025 PatSnap. All rights reserved.Legal|Privacy policy|Modern Slavery Act Transparency Statement|Sitemap|About US| Contact US: help@patsnap.com