A three-degree-of-freedom spherical hybrid magnetic bearing with axial self-loop
A technology of hybrid magnetic bearings and degrees of freedom, applied in the direction of shafts and bearings, bearings, shafts, etc., can solve the problems of limited rotor speed, large volume, and gyro effect, which is conducive to high-speed operation, small size, and convenient Controlling and Analyzing Effects
- Summary
- Abstract
- Description
- Claims
- Application Information
AI Technical Summary
Problems solved by technology
Method used
Image
Examples
Embodiment Construction
[0027] see figure 1 The whole of the present invention is a structure that is symmetrical up and down along the axial direction. The middle of the axial direction is the rotor 7. Outside the rotor 7, the upper axial stator 11, the upper annular permanent magnet 31 and the radial stator are coaxially sleeved in order from top to bottom. 4. The lower annular permanent magnet 32 and the lower axial stator 12 . Moreover, the outer diameters of the upper axial stator 11 , the upper annular permanent magnet 31 , the radial stator 4 , the lower annular permanent magnet 32 , and the lower axial stator 12 are the same. The radial stator 4 is sleeved outside the middle of the rotor 7, the upper axial stator 11 and the lower axial stator 12 have the same structure and are arranged symmetrically up and down along the center of the rotor 7, and the upper annular permanent magnet 31 and the lower annular permanent magnet 32 The structure is completely They are the same and arranged s...
PUM
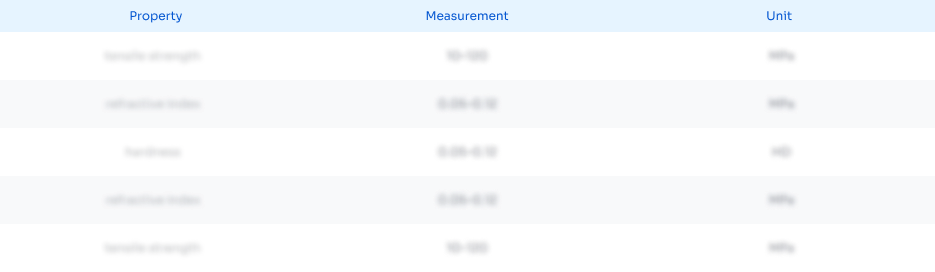
Abstract
Description
Claims
Application Information

- R&D
- Intellectual Property
- Life Sciences
- Materials
- Tech Scout
- Unparalleled Data Quality
- Higher Quality Content
- 60% Fewer Hallucinations
Browse by: Latest US Patents, China's latest patents, Technical Efficacy Thesaurus, Application Domain, Technology Topic, Popular Technical Reports.
© 2025 PatSnap. All rights reserved.Legal|Privacy policy|Modern Slavery Act Transparency Statement|Sitemap|About US| Contact US: help@patsnap.com