A Workspace Solution Method for Flexible Supported Industrial Robots
A technology for industrial robots and workspaces, applied in instruments, manipulators, manufacturing tools, etc., can solve problems such as terminal accuracy deterioration, terminal large workspace, system vibration, etc., and achieve the effect of suppressing disturbances
- Summary
- Abstract
- Description
- Claims
- Application Information
AI Technical Summary
Problems solved by technology
Method used
Image
Examples
Embodiment Construction
[0033] The present invention will be described in further detail below in conjunction with the accompanying drawings and specific embodiments.
[0034] Introduction to basic principles
[0035] (1) Instructions for solving kinematic position Jacobian matrix and position Hessian matrix
[0036] Using the D-H homogeneous coordinate change rule to obtain the mutual mapping matrix between the end coordinates and the base coordinates of industrial robots The position Jacobian matrix can be expressed as:
[0037]
[0038] The Hessian matrix H is to use the Jacobian matrix to re-align [θ 1 ,θ 2 ,θ 3 ] Derivation:
[0039]
[0040] (2) The local condition number (abbreviation: KCI) solution method of the industrial robot kinematic index position Jacobian matrix
[0041] Index range 1≤KCImin Indicates the minimum singular value of the position Jacobian matrix, σ max Indicates the largest singular value of the positional Jacobian matrix. The KCI index is usually aimed a...
PUM
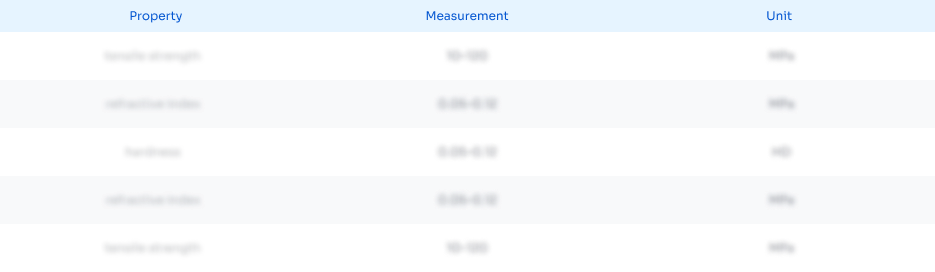
Abstract
Description
Claims
Application Information

- R&D
- Intellectual Property
- Life Sciences
- Materials
- Tech Scout
- Unparalleled Data Quality
- Higher Quality Content
- 60% Fewer Hallucinations
Browse by: Latest US Patents, China's latest patents, Technical Efficacy Thesaurus, Application Domain, Technology Topic, Popular Technical Reports.
© 2025 PatSnap. All rights reserved.Legal|Privacy policy|Modern Slavery Act Transparency Statement|Sitemap|About US| Contact US: help@patsnap.com