Light-weight automobile damping rubber sheet and manufacturing process and device thereof
A production process and lightweight technology, applied in adhesives, vehicle parts, transportation and packaging, etc., can solve the problems of high density and mass of damping film, and achieve the effects of increasing sound-absorbing area, alleviating vibration, and enhancing absorption capacity
- Summary
- Abstract
- Description
- Claims
- Application Information
AI Technical Summary
Problems solved by technology
Method used
Image
Examples
Embodiment 1
[0047] Such as figure 1As shown, a lightweight automotive damping film, including a bonding layer 1 and a reinforcing layer 2, a number of flexible columns 3 are arranged between the bonding layer 1 and the reinforcing layer 2, and the flexible columns 3 are perpendicular to the bonding layer 1 and the reinforcing layer 2 .
[0048] In this embodiment, several flexible columns 3 are arranged between the adhesive layer 1 and the reinforcement layer 2, and the adhesive layer 1 and the reinforcement layer 2 form a cavity through the support of the flexible columns 3. The present invention adopts a new structure, and the cavity The existence of finiteness reduces the density and quality of the damping film. At the same time, due to the existence of the cavity, the damping film can play a better effect of cold and heat insulation. Several flexible columns 3 in the cavity increase the sound absorption of the damping film. area, so that the damping film can have a better absorption ...
Embodiment 2
[0054] Further, the bonding layer 1 is pressure-sensitive adhesive, the reinforcing layer 2 is made of laminated aluminum foil, and the material of the flexible column 3 includes PP and / or EPDM and / or TPE.
[0055] In this embodiment, the bonding layer 1 is made of pressure-sensitive adhesive, which has high viscosity and will not be degummed during use, and the bonding process of the pressure-sensitive adhesive is convenient, making the damping film easy to use and strengthening Layer 2 is made of aluminum foil. The aluminum foil has excellent corrosion resistance and plasticity. At the same time, the aluminum foil has high strength, high tensile strength, and low tear strength. It is suitable for the application scene of damping film. The glue attached to the surface of the aluminum foil can make The flexible column 3 is bonded to the aluminum foil, which simplifies the production process.
[0056] The flexible column 3 is made by mixing PP and / or EPDM and / or TPE. Since the ...
Embodiment 3
[0058] Such as Figure 1 ~ Figure 3 As shown, a manufacturing process of a lightweight automobile damping film is used to produce a lightweight automobile damping film,
[0059] Step 1: heating the raw material, extruding the raw material into the mold after heating, and making the flexible column 3 after cooling,
[0060] Step 2: arrange the flexible pillars 3, and press several arranged flexible pillars 3 onto the bonding layer 1,
[0061] Step 3: Press the reinforcing layer 2 onto the end of the flexible column 3 farther from the adhesive layer 1 .
[0062] In this embodiment, when making lightweight automobile damping film, the raw materials are melted first, and the raw materials are squeezed into the mold, and the flexible columns 3 are formed after the raw materials are cooled. The arrangement is regular, and the arranged flexible columns 3 are pressed onto the adhesive layer 1, and then the reinforcing layer 2 is laid and combined with the adhesive layer 1 to compres...
PUM
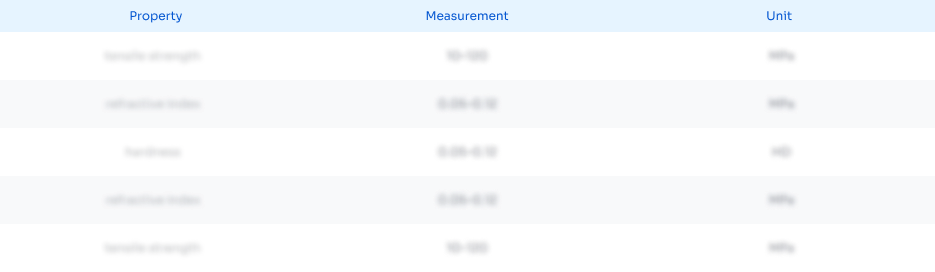
Abstract
Description
Claims
Application Information

- R&D Engineer
- R&D Manager
- IP Professional
- Industry Leading Data Capabilities
- Powerful AI technology
- Patent DNA Extraction
Browse by: Latest US Patents, China's latest patents, Technical Efficacy Thesaurus, Application Domain, Technology Topic, Popular Technical Reports.
© 2024 PatSnap. All rights reserved.Legal|Privacy policy|Modern Slavery Act Transparency Statement|Sitemap|About US| Contact US: help@patsnap.com