CLP process based method for removing and recycling mercury and regenerating adsorbent in coal-fired flue gas
A technology of adsorbent regeneration and coal-fired flue gas, which is applied in the field of flue gas purification, can solve the problems of resources not being recycled, and achieve the effects of reducing mercury removal costs, long use time, and low energy and loss
- Summary
- Abstract
- Description
- Claims
- Application Information
AI Technical Summary
Problems solved by technology
Method used
Image
Examples
Embodiment 1
[0026] refer to figure 1 , a method for mercury removal and recovery and adsorbent regeneration in coal-fired flue gas based on CLP process, comprising the following steps:
[0027] S1. Mercury oxidation adsorption removal process: Mercury-containing flue gas enters the mercury oxidation adsorption removal reactor 3 from the first air inlet 1 at a speed of 5m / s, contacts and reacts with the metal compound carrier adsorbent, and mercury oxidation adsorption removal The internal temperature of the reactor 3 is 80°C, and the clean flue gas after mercury removal is discharged from the gas outlet 14;
[0028] The elemental mercury in the flue gas is oxidized to divalent mercury, which stays on the surface of the carrier adsorbent to form a mercury-rich adsorbent. The volume ratio of the metal compound carrier adsorbent to the mercury-containing flue gas is 100mg / m 3 ; The metal compound carrier adsorbent used in S1 is metal oxide MnO X ;
[0029] S2. Mercury desorption recovery ...
Embodiment 2
[0033] refer to figure 1 , a method for mercury removal and recovery and adsorbent regeneration in coal-fired flue gas based on CLP process, comprising the following steps:
[0034] S1. Mercury oxidation adsorption removal process: Mercury-containing flue gas enters the mercury oxidation adsorption removal reactor 3 from the first air inlet 1 at a speed of 5m / s, contacts and reacts with the metal compound carrier adsorbent, and mercury oxidation adsorption removal The internal temperature of the reactor 3 is 90°C, and the clean flue gas after mercury removal is discharged from the gas outlet 14;
[0035] The elemental mercury in the flue gas is oxidized to divalent mercury, which stays on the surface of the carrier adsorbent to form a mercury-rich adsorbent. The volume ratio of the metal compound carrier adsorbent to the mercury-containing flue gas is 200mg / m3; the metal compound used in S1 The carrier adsorbent is metal oxide CoO X ;
[0036] S2. Mercury desorption recover...
Embodiment 3
[0040] refer to figure 1 , a method for removing and recovering mercury from coal-fired flue gas and regenerating an adsorbent based on a CLP process, comprising the following steps:
[0041] S1. Mercury oxidative adsorption and removal process: The mercury-containing flue gas enters the mercury oxidative adsorption and removal reactor 3 from the first air inlet 1 at a speed of 5 m / s and contacts and reacts with the metal compound carrier adsorbent, and the mercury oxidative adsorption and removal The internal temperature of the reactor 3 is 120°C, and the clean flue gas after mercury removal is discharged from the gas outlet 14;
[0042] The elemental mercury in the flue gas is oxidized to divalent mercury, which stays on the surface of the carrier adsorbent to form a mercury-rich adsorbent. The ratio of the metal compound carrier adsorbent to the volume of mercury-containing flue gas is 1000 mg / m 3 ; The metal compound carrier adsorbent used in S1 is metal sulfide FeS X ; ...
PUM
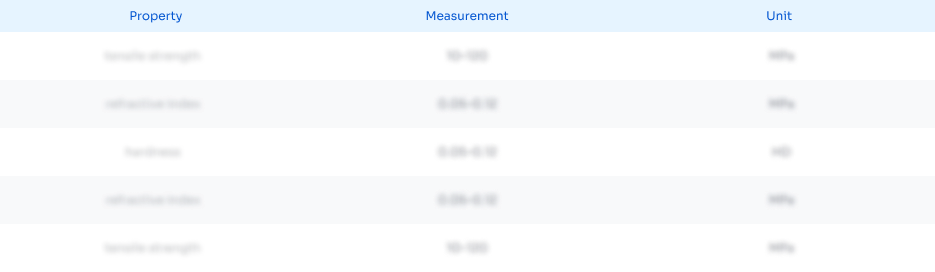
Abstract
Description
Claims
Application Information

- R&D Engineer
- R&D Manager
- IP Professional
- Industry Leading Data Capabilities
- Powerful AI technology
- Patent DNA Extraction
Browse by: Latest US Patents, China's latest patents, Technical Efficacy Thesaurus, Application Domain, Technology Topic, Popular Technical Reports.
© 2024 PatSnap. All rights reserved.Legal|Privacy policy|Modern Slavery Act Transparency Statement|Sitemap|About US| Contact US: help@patsnap.com