Steel-aluminum composite conductor rail and manufacturing method thereof
A steel-aluminum composite and conductive rail technology, applied in the field of conductive rails, can solve the problems of large cross-sectional shape limitations, large cross-sectional shape limitations, inconsistent lengths of steel and aluminum, etc., to reduce the penetration resistance of the wear-resistant layer and save energy The effect is obvious and the effect of reducing the conduction resistance
- Summary
- Abstract
- Description
- Claims
- Application Information
AI Technical Summary
Problems solved by technology
Method used
Image
Examples
Embodiment 1
[0026] A steel-aluminum composite conductor rail, such as figure 1 As shown, it includes an aluminum substrate 1, a plate-shaped wear-resistant body 2 is installed on the upper end of the aluminum substrate 1, and wear-resistant body slots are processed on both sides of the upper end of the aluminum substrate 1. The wear-resistant body slot is a groove, and the wear-resistant body includes two The wear-resistant monomer is made of stainless steel with a thickness of 4mm. The cross-section of the wear-resistant monomer is L-shaped. The lower end of the wear-resistant monomer is bent inward to form a bending part 8, and the edge of the bending part 8 The wear-resistant single tooth 2A is uniformly processed. The cross-section of the wear-resistant single tooth 2A is triangular. There is a first groove matching the wear-resistant single tooth. In this embodiment, the first groove is formed by the wear-resistant single tooth extrusion process of the wear-resistant single body to t...
PUM
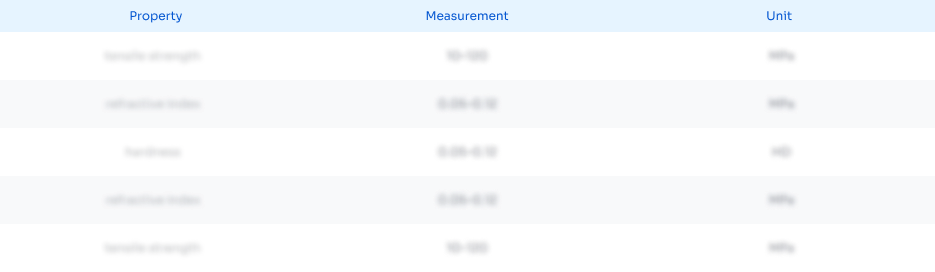
Abstract
Description
Claims
Application Information

- R&D
- Intellectual Property
- Life Sciences
- Materials
- Tech Scout
- Unparalleled Data Quality
- Higher Quality Content
- 60% Fewer Hallucinations
Browse by: Latest US Patents, China's latest patents, Technical Efficacy Thesaurus, Application Domain, Technology Topic, Popular Technical Reports.
© 2025 PatSnap. All rights reserved.Legal|Privacy policy|Modern Slavery Act Transparency Statement|Sitemap|About US| Contact US: help@patsnap.com