Manufacturing process of wear-resistant flax composite fabric
A technology for composite fabric and production process, applied in the field of fabric technology, can solve the problems of low process work efficiency, increased demand, low production quality, etc., and achieve the effects of improving production quality, processing efficiency and convenient operation.
- Summary
- Abstract
- Description
- Claims
- Application Information
AI Technical Summary
Problems solved by technology
Method used
Image
Examples
Embodiment Construction
[0032] The following are specific embodiments of the present invention in conjunction with the accompanying drawings to further describe the technical solutions of the present invention, but the present invention is not limited to these embodiments.
[0033] Such as Figure 1-4 As shown, a manufacturing process of wear-resistant linen composite fabric includes the following steps:
[0034] a. Weaving of base fabric: weave polyester yarn into base fabric, and apply wear-resistant coating on the base fabric through a coating machine;
[0035] b. Face cloth knitting: knit wool and linen into face cloth;
[0036] c. Pre-treatment of face cloth: including singeing and biological enzyme treatment; singeing and biological enzyme treatment are common technical means in the existing processing technology.
[0037] d. Dyeing the face cloth: Put the face cloth in step c into the dyeing vat for dyeing, and the dyeing time is 50-60 minutes;
[0038] e. Drying of the face cloth: Put the face cloth in...
PUM
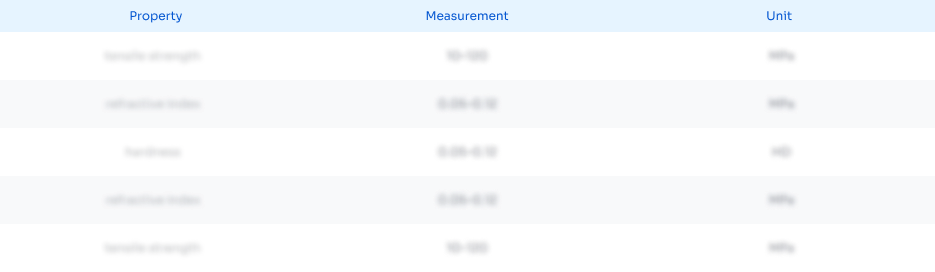
Abstract
Description
Claims
Application Information

- R&D
- Intellectual Property
- Life Sciences
- Materials
- Tech Scout
- Unparalleled Data Quality
- Higher Quality Content
- 60% Fewer Hallucinations
Browse by: Latest US Patents, China's latest patents, Technical Efficacy Thesaurus, Application Domain, Technology Topic, Popular Technical Reports.
© 2025 PatSnap. All rights reserved.Legal|Privacy policy|Modern Slavery Act Transparency Statement|Sitemap|About US| Contact US: help@patsnap.com