Gantry crane and steering method thereof
A gantry crane and flange technology, applied in the field of machinery, can solve the problems of difficult steering of gantry cranes
- Summary
- Abstract
- Description
- Claims
- Application Information
AI Technical Summary
Problems solved by technology
Method used
Image
Examples
Embodiment 1
[0076] Such as figure 1 As shown, the gantry crane includes a door-shaped hoisting body 1, and also includes a power mechanism 2, four slewing mechanisms 3, two walking beams 4, two jacking mechanisms 5 and four wheels 6; Beams 4 are respectively arranged on the lower ends of the two supporting columns of the door-shaped hoisting body 1; in the middle part of the walking beam 4 and below the walking beam 4, a jacking mechanism 5 is arranged; Below the walking beam 4, one said slewing mechanism 3 is respectively arranged on both sides of said jacking mechanism 5; four said wheels 6 are mounted on four said slewing mechanisms 3 one by one; said jacking mechanism 5. It is used to jack up a correspondingly connected current walking beam 4 so that the two wheels 6 connected to the current walking beam 4 through the slewing mechanism 3 are out of contact with the ground; The current walking beam 4 is lowered so that the two wheels 6 connected to the current walking beam 4 through t...
Embodiment 2
[0080] Please refer to figure 2 , the second embodiment is basically the same as the first embodiment, the similarities will not be repeated, the difference is that: the walking beam 4 is parallel to the width direction of the hoisting body 1; the gantry crane also includes: four auxiliary supports arm 7; wherein, the two ends of the walking beam 4 are respectively connected to the first end of one of the auxiliary support arms 7; the second ends of the four auxiliary support arms 7 can be distributed in a rectangular shape, and the present The length of the rectangle is the same as the distance between the two walking beams 4 , and the width of the rectangle presented is larger than the width of the hoisting body.
[0081] In the second embodiment, since the gantry crane has a large external dimension, but its width is relatively small relative to its length and height, an auxiliary support arm is provided at the two ends of the walking beam respectively, and the auxiliary s...
Embodiment 3
[0083] Please refer to figure 2 , this third embodiment can be realized based on the foregoing embodiments, and in this third embodiment, the auxiliary support arm 7 is detachably connected to the end of the walking beam 4 .
[0084] In the third embodiment, the auxiliary support arm is detachably connected to the end of the walking beam. When the gantry crane runs and turns in a narrower area, the auxiliary support arm can be disassembled to reduce the width of the gantry crane, so as to meet the needs of the gantry crane in a more narrow area. Space requirements for operation and steering in narrow areas.
PUM
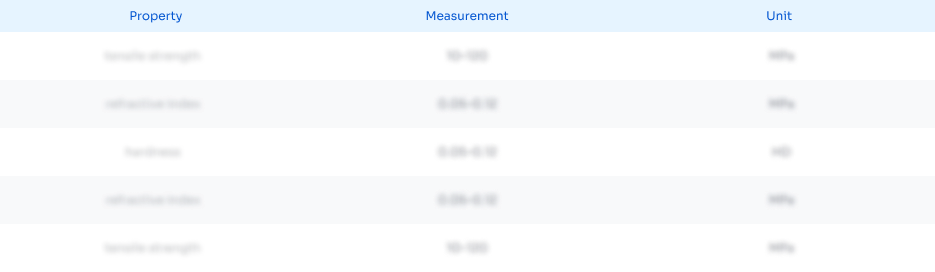
Abstract
Description
Claims
Application Information

- Generate Ideas
- Intellectual Property
- Life Sciences
- Materials
- Tech Scout
- Unparalleled Data Quality
- Higher Quality Content
- 60% Fewer Hallucinations
Browse by: Latest US Patents, China's latest patents, Technical Efficacy Thesaurus, Application Domain, Technology Topic, Popular Technical Reports.
© 2025 PatSnap. All rights reserved.Legal|Privacy policy|Modern Slavery Act Transparency Statement|Sitemap|About US| Contact US: help@patsnap.com