A kind of reduction prepares the method for triphenylphosphine
A technology of triphenylphosphine and triphenylphosphine oxide, which is applied in the field of reducing and preparing triphenylphosphine, which can solve the problems of harsh reaction conditions, rare reaction raw materials, and non-renewable reducing agent, and achieve less catalyst amount and high catalytic efficiency , The effect of less catalyst dosage
- Summary
- Abstract
- Description
- Claims
- Application Information
AI Technical Summary
Problems solved by technology
Method used
Examples
Embodiment 1
[0043] Put 27.8g of triphenylphosphine oxide, 88.2g of diphenylphosphine chloride (the mass ratio of the two is 1:3.17), and 0.56g of trifluoromethanesulfonic acid (triphenylphosphine oxide) into the 250mL reaction flask replaced by nitrogen. 2% of the mass), the temperature is raised to 150°C, and the temperature is kept for 12h. After cooling to room temperature, turn on the vacuum pump. After the vacuum degree reaches 0.098Mpa, the temperature is slowly raised to intercept the mixture of diphenylphosphine chloride and diphenylphosphinyl chloride. After the high boiler is cooled, put in 50g of toluene, wash with saturated sodium carbonate to neutrality, wash the organic layer twice with deionized water, separate the organic layer, distill to recover the toluene, put 30g of ethanol in the bottle, and recrystallize to obtain three Phenylphosphine was 23.6g, the yield was 90%, and the content detected by HPLC was 98.7%.
Embodiment 2
[0045] Put 27.8g of triphenylphosphine oxide, 71.6g of phenylphosphine dichloride (the mass ratio of the two is 1:2.58), 0.56g of trifluoromethanesulfonic acid (triphenylphosphine oxide) into the 250mL reaction flask after nitrogen replacement. 2% of the mass), the temperature is raised to 150°C, and the temperature is kept for 12h. After cooling to room temperature, turn on the vacuum pump. After the vacuum degree reaches 0.098Mpa, the temperature is slowly raised to intercept the mixture of phenylphosphonium dichloride and phenylphosphonic dichloride. After the high boiler is cooled, put in 50g of toluene, wash with saturated sodium carbonate to neutrality, wash the organic layer twice with deionized water, separate the organic layer, distill to recover the toluene, put 30g of ethanol in the bottle, and recrystallize to obtain three Phenylphosphine was 21.6g, the yield was 82.4%, and the content detected by HPLC was 98.5%.
Embodiment 3
[0047] Put 27.8g of triphenylphosphine oxide, 88.2g of diphenylphosphine chloride (the mass ratio of the two is 1:3.17), and 0.56g of diphenylphosphonic acid (triphenylphosphine oxide) into the 250mL reaction flask replaced by nitrogen. 2% of the mass), the temperature is raised to 150°C, and the temperature is kept for 12h. After cooling to room temperature, turn on the vacuum pump. After the vacuum degree reaches 0.098Mpa, the temperature is slowly raised to intercept the mixture of diphenylphosphine chloride and diphenylphosphinyl chloride. After the high boiler is cooled, put in 50g of toluene, wash with saturated sodium carbonate to neutrality, wash the organic layer twice with deionized water, separate the organic layer, distill to recover the toluene, put 30g of ethanol in the bottle, and recrystallize to obtain three Phenylphosphine 18.4g, the yield was 70%, and the content detected by HPLC was 97.8%.
PUM
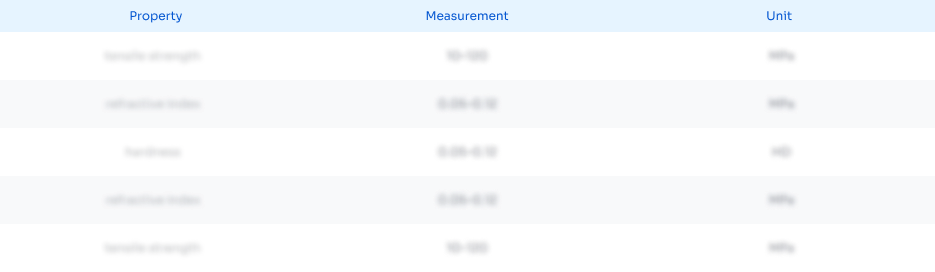
Abstract
Description
Claims
Application Information

- R&D
- Intellectual Property
- Life Sciences
- Materials
- Tech Scout
- Unparalleled Data Quality
- Higher Quality Content
- 60% Fewer Hallucinations
Browse by: Latest US Patents, China's latest patents, Technical Efficacy Thesaurus, Application Domain, Technology Topic, Popular Technical Reports.
© 2025 PatSnap. All rights reserved.Legal|Privacy policy|Modern Slavery Act Transparency Statement|Sitemap|About US| Contact US: help@patsnap.com