Laser 3D printing finite element simulation method
A technology of 3D printing and simulation method, which is applied in the field of finite element simulation of laser 3D printing, which can solve the problem of not fully reflecting the single-layer multi-channel thermal effect of laser printing.
- Summary
- Abstract
- Description
- Claims
- Application Information
AI Technical Summary
Problems solved by technology
Method used
Image
Examples
Embodiment Construction
[0025] The specific embodiment of the present invention will be further described in detail below in conjunction with the accompanying drawings.
[0026] It should be noted that, in the following specific embodiments, when describing the embodiments of the present invention in detail, in order to clearly show the structure of the present invention for the convenience of description, the structures in the drawings are not drawn according to the general scale, and are drawn Partial magnification, deformation and simplification are included, therefore, it should be avoided to be interpreted as a limitation of the present invention.
[0027] This embodiment takes the simulated coaxial powder feeding metal laser 3D printing technology as an example. For the actual coaxial powder feeding laser 3D printing device, please refer to figure 1 In the figure, 1 is a vacuum glove box, 2 is a laser cladding head, 3 is a laser beam, 4 is a metal powder, 5 is a component, 6 is a substrate, 7 i...
PUM
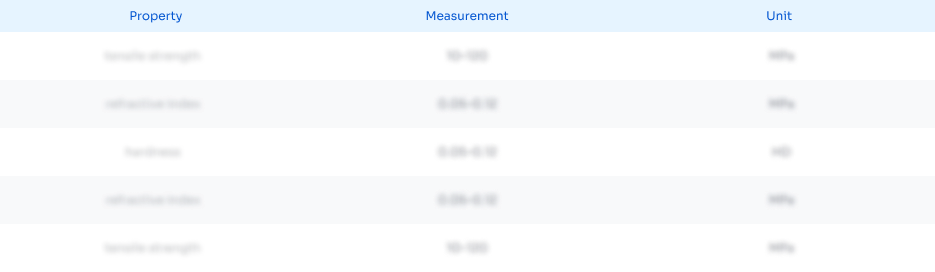
Abstract
Description
Claims
Application Information

- Generate Ideas
- Intellectual Property
- Life Sciences
- Materials
- Tech Scout
- Unparalleled Data Quality
- Higher Quality Content
- 60% Fewer Hallucinations
Browse by: Latest US Patents, China's latest patents, Technical Efficacy Thesaurus, Application Domain, Technology Topic, Popular Technical Reports.
© 2025 PatSnap. All rights reserved.Legal|Privacy policy|Modern Slavery Act Transparency Statement|Sitemap|About US| Contact US: help@patsnap.com