Towel printing process
A printing process and towel technology, applied in printing, printing machines, rotary printing machines, etc., can solve the problems of losing the advantages and characteristics of printing products, product details and fineness defects, and inability to achieve consistent rules, etc., to improve printing efficiency , meet the color and sensory requirements, and reduce the effect of labor intensity
- Summary
- Abstract
- Description
- Claims
- Application Information
AI Technical Summary
Problems solved by technology
Method used
Examples
Embodiment 1
[0014] The towel printing process of the present embodiment comprises the following steps:
[0015] (1) Color separation: first carry out computer color separation, and then use a laser phototypesetting machine with a resolution ≥ 2000dpi to output the film for use in plate making;
[0016] (2) Plate making: Use ≥ 350 mesh polyester screen as the support body, tighten the screen on the screen frame, and then apply photosensitive glue to form a photosensitive plate film, and then seal the film on the plate film for printing. exposed, developed;
[0017] (3) Sizing: sizing the fabric, the slurry is made by stirring and mixing the following components by weight percentage at a speed of 2000r / min: 3wt% diisooctyl sodium succinate sulfonate solution, 3wt% fatty salt softener and the balance of acrylic resin;
[0018] (4) Scratch printing: cover the screen plate in step (2) on the printed fabric, and then scrape with a pressure of 4kg for 3 seconds;
[0019] (5) Post-processing: ...
Embodiment 2
[0021] The towel printing process of the present embodiment comprises the following steps:
[0022] (1) Color separation: first carry out computer color separation, and then use a laser phototypesetting machine with a resolution ≥ 2000dpi to output the film for use in plate making;
[0023] (2) Plate making: Use ≥ 350 mesh polyester screen as the support body, tighten the screen on the screen frame, and then apply photosensitive glue to form a photosensitive plate film, and then seal the film on the plate film for printing. exposed, developed;
[0024] (3) Sizing: sizing the fabric, the slurry is made by stirring and mixing the following components by weight percentage at a speed of 2200r / min: 5wt% diisooctyl sodium succinate sulfonate solution, 5wt% fatty salt softener and the balance of acrylic resin;
[0025] (4) Scratch printing: cover the screen plate in step (2) on the printed fabric, and then scrape with a pressure of 6kg for 5 seconds;
[0026] (5) Post-processing: ...
Embodiment 3
[0028] The towel printing process of the present embodiment comprises the following steps:
[0029] (1) Color separation: first carry out computer color separation, and then use a laser phototypesetting machine with a resolution ≥ 2000dpi to output the film for use in plate making;
[0030] (2) Plate making: Use ≥ 350 mesh polyester screen as the support body, tighten the screen on the screen frame, and then apply photosensitive glue to form a photosensitive plate film, and then seal the film on the plate film for printing. exposed, developed;
[0031] (3) Sizing: sizing the fabric, the slurry is made by stirring and mixing the following components by weight percentage at a speed of 2100r / min: 4wt% diisooctyl sodium succinate sulfonate solution, 4wt% fatty salt softener and the balance of acrylic resin;
[0032] (4) Scratch printing: cover the screen plate in step (2) on the printed fabric, and then scrape with a pressure of 5kg for 4 seconds;
[0033] (5) Post-processing: ...
PUM
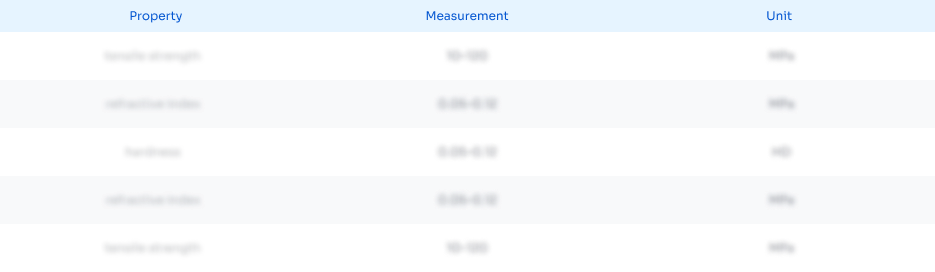
Abstract
Description
Claims
Application Information

- R&D Engineer
- R&D Manager
- IP Professional
- Industry Leading Data Capabilities
- Powerful AI technology
- Patent DNA Extraction
Browse by: Latest US Patents, China's latest patents, Technical Efficacy Thesaurus, Application Domain, Technology Topic, Popular Technical Reports.
© 2024 PatSnap. All rights reserved.Legal|Privacy policy|Modern Slavery Act Transparency Statement|Sitemap|About US| Contact US: help@patsnap.com