Automatic measuring compensation method and correction device for five-axis machine tool structure errors
An automatic measurement and axis error technology, applied in automatic control devices, feeding devices, metal processing machinery parts, etc., can solve the problems of inability to achieve error compensation, time-consuming and labor-intensive, and low efficiency.
- Summary
- Abstract
- Description
- Claims
- Application Information
AI Technical Summary
Problems solved by technology
Method used
Image
Examples
Embodiment Construction
[0025] In order to have a clearer understanding of the technical features, purposes and effects of the present invention, the specific implementation manners of the present invention will now be described with reference to the accompanying drawings.
[0026] The invention proposes a method for automatically measuring and compensating the structure error of a five-axis machine tool, which only needs to use a correction block and a measuring head, and has a very simple structure. The error automatic measurement compensation is realized by using the error automatic measurement program and the calculation compensation model. Since the whole process is semi-automatic, the operation is simple for machine tool debuggers and maintenance personnel, and the five-axis linkage structural error measurement and compensation can be quickly completed with just a few instructions.
[0027] In the preferred embodiment of the present invention, please refer to figure 1 As shown, it is a schemat...
PUM
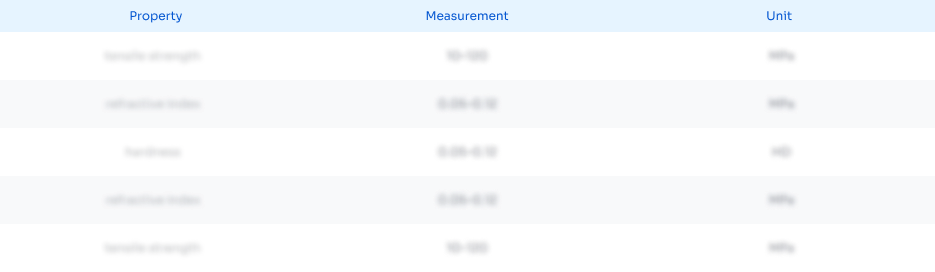
Abstract
Description
Claims
Application Information

- R&D Engineer
- R&D Manager
- IP Professional
- Industry Leading Data Capabilities
- Powerful AI technology
- Patent DNA Extraction
Browse by: Latest US Patents, China's latest patents, Technical Efficacy Thesaurus, Application Domain, Technology Topic, Popular Technical Reports.
© 2024 PatSnap. All rights reserved.Legal|Privacy policy|Modern Slavery Act Transparency Statement|Sitemap|About US| Contact US: help@patsnap.com