Joint surface error and joint surface tolerance optimization method for machine tool fixture component
A technology of machine tool fixtures and optimization methods, which is applied in computer control, instruments, simulators, etc., can solve problems such as affecting calculation accuracy and trimming accuracy, and difficult to achieve automation, so as to improve cost performance, improve design efficiency, and optimize the design process. Effect
- Summary
- Abstract
- Description
- Claims
- Application Information
AI Technical Summary
Problems solved by technology
Method used
Image
Examples
Embodiment Construction
[0038] The present invention is described in detail below, and the present implementation example implements under the premise of the technical solution of the present invention, and provides a detailed implementation process, but the scope of protection of the present invention is not limited to the subordinate embodiments.
[0039] The method of the present invention is: by optimizing the part surface error (part tolerance and assembly error) parameters of each part of the fixture assembly, the overall assembly accuracy of the fixture assembly and the dynamic balance accuracy under the condition of clamping the workpiece are improved; after the surface error optimization of the parts is completed, The error parameters are sampled in the tolerance and error parameter space, and the 3D model set of the fixture assembly that meets the sampling parameters is established; through the statistics of the dynamic unbalance of the fixture assembly, the expectation of the dynamic unbalance...
PUM
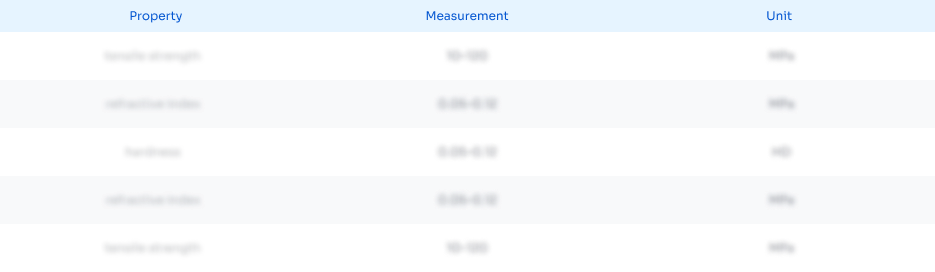
Abstract
Description
Claims
Application Information

- Generate Ideas
- Intellectual Property
- Life Sciences
- Materials
- Tech Scout
- Unparalleled Data Quality
- Higher Quality Content
- 60% Fewer Hallucinations
Browse by: Latest US Patents, China's latest patents, Technical Efficacy Thesaurus, Application Domain, Technology Topic, Popular Technical Reports.
© 2025 PatSnap. All rights reserved.Legal|Privacy policy|Modern Slavery Act Transparency Statement|Sitemap|About US| Contact US: help@patsnap.com