A Grab Bucket Ultrasonic Positioning Method
A positioning method, ultrasonic technology, applied in positioning, using ultrasonic/sonic wave/infrasonic wave, radio wave measurement system, etc., can solve problems such as easy breakage of cables, mechanical wear of encoders, measurement errors, etc., so as to facilitate centralized monitoring and engineering Small amount of effect
- Summary
- Abstract
- Description
- Claims
- Application Information
AI Technical Summary
Problems solved by technology
Method used
Image
Examples
Embodiment
[0022] Example: such as figure 1 As shown, this embodiment specifically relates to a grab bucket ultrasonic positioning method, which is used to locate the position of the grab bucket; in this embodiment, two grab buckets 1 to be positioned are suspended above the garbage pool 3 by the garbage crane 2 , the garbage pool 3 and the space above it are the operating area of the grab bucket 1 to be positioned; the garbage pool is 100m long and 25m wide; the method specifically includes the following steps:
[0023] 1) if figure 1 , 2 As shown, a synchronization component 4 is installed, an ultrasonic transmitter 6 is installed on the grab bucket 1 to be positioned, and a positioning calculation device 7 and at least three ultrasonic receivers 5 are installed around the operating area of the grab bucket to be positioned.
[0024] 1.1) If figure 1 , 2 As shown, the synchronization assembly 4 includes a synchronization signal transmitting module 8 and two synchronization trigg...
Embodiment 2
[0043] Embodiment 2: as Figure 4 , 5 As shown, the main difference between this embodiment and Embodiment 1 is that the synchronization signal in this embodiment is a radio pulse signal; in this embodiment, the synchronization signal transmitting module 8 includes a timing trigger control circuit 10 and a wireless pulse signal transmitter connected to each other 18; the wireless pulse signal transmitter 18 can send a synchronous signal under the control of the timing trigger control circuit 10; in order to be compatible with the synchronous signal transmitting module 8, the synchronous signal receiving module 12 in the synchronous triggering module 9 is a wireless pulse signal receiving device.
PUM
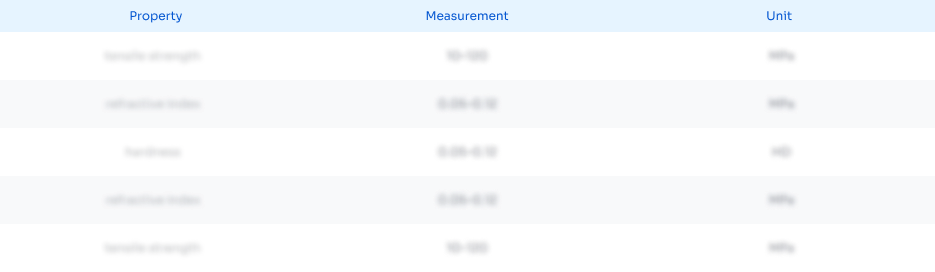
Abstract
Description
Claims
Application Information

- Generate Ideas
- Intellectual Property
- Life Sciences
- Materials
- Tech Scout
- Unparalleled Data Quality
- Higher Quality Content
- 60% Fewer Hallucinations
Browse by: Latest US Patents, China's latest patents, Technical Efficacy Thesaurus, Application Domain, Technology Topic, Popular Technical Reports.
© 2025 PatSnap. All rights reserved.Legal|Privacy policy|Modern Slavery Act Transparency Statement|Sitemap|About US| Contact US: help@patsnap.com