Plastic particle mixing dryer
A stirring dryer and plastic granule technology, which is applied in the field of plastic manufacturing and processing, can solve the problems of poor drying effect of plastic granules, etc.
- Summary
- Abstract
- Description
- Claims
- Application Information
AI Technical Summary
Problems solved by technology
Method used
Image
Examples
Embodiment 1
[0030] The first embodiment of the present invention is as figure 1 As shown, a plastic particle stirring dryer is disclosed, comprising a frame 100 fixed to the ground, a drying box is installed on the frame 100, the drying box includes a cylindrical material barrel 101 and a conical discharge hopper 102, and the conical discharge hopper 102 is arranged below the material barrel 101, the top of the material barrel 101 is provided with a cover, the cover is provided with a feed hopper 103 and an opening for the shaft 200 to pass through, and the top of the rotating shaft 200 exposes the material barrel 101; on the inner wall of the material barrel 101 There are a plurality of columnar protrusions 104 with different lengths, and a spiral blade 201 is provided on the rotating shaft 200 inside the barrel 101; an end cam 202 is provided on the top of the rotating shaft 200, and a through hole communicating with the end cam 202 is provided inside the rotating shaft 200 203; the rot...
Embodiment 2
[0034] The difference from the first embodiment is that the columnar projections 104 in the second embodiment are arranged on a drum 105, such as image 3 As shown, the rotating drum 105 is meshed with the rotating shaft 200 through planetary gears, the inner wall of the rotating drum 105 is provided with a ring gear 106 near the top of the barrel 101, the sun gear 108 is installed on the rotating shaft 200, and the planet carrier 109 is connected to the top of the barrel 101. The specific connection method is as Figure 4 As shown; the rotating cylinder 105 is arranged inside the material barrel 101, and the rotating cylinder 105 is connected with the material barrel 101 in rotation, and the specific method is as follows Figure 5 As shown, an annular protrusion 110 is provided at the connection between the material barrel 101 and the discharge hopper 102, and a spherical groove is arranged on the annular protrusion 110. Several balls 111 are placed in the spherical groove, a...
PUM
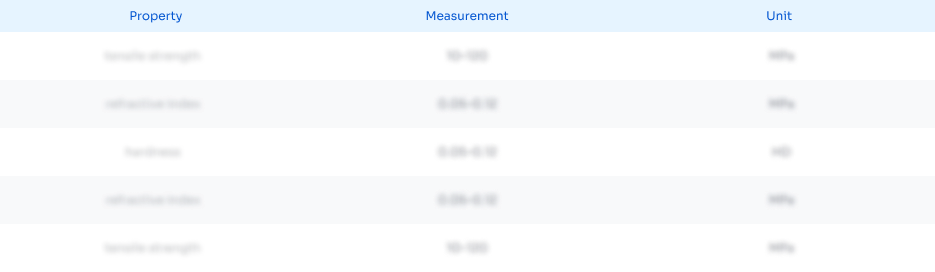
Abstract
Description
Claims
Application Information

- R&D
- Intellectual Property
- Life Sciences
- Materials
- Tech Scout
- Unparalleled Data Quality
- Higher Quality Content
- 60% Fewer Hallucinations
Browse by: Latest US Patents, China's latest patents, Technical Efficacy Thesaurus, Application Domain, Technology Topic, Popular Technical Reports.
© 2025 PatSnap. All rights reserved.Legal|Privacy policy|Modern Slavery Act Transparency Statement|Sitemap|About US| Contact US: help@patsnap.com