A lithium battery winding device and winding process
A technology of winding device and pressurizing device, which is applied in the direction of secondary batteries, circuits, electrical components, etc., can solve the problems of increasing manufacturing costs, scrapping, short-circuiting diaphragms, etc., and achieve the goal of improving product rate performance, reducing costs, and reducing difficulty Effect
- Summary
- Abstract
- Description
- Claims
- Application Information
AI Technical Summary
Problems solved by technology
Method used
Image
Examples
Embodiment 1
[0055] see Figure 4 , Figure 4 It is a flow chart of the winding process of the present invention. Such as Figure 4 As shown, the production process of the positive electrode sheet is: coating the positive electrode, cutting the positive electrode sheet, making and baking the positive electrode sheet; the production process of the negative electrode sheet is: coating the negative electrode sheet, cutting the negative electrode sheet, making and baking the negative electrode sheet , the baked positive electrode sheet, the separator and the baked negative electrode sheet are laminated and then wound.
[0056] The present invention improves the process by changing the current conventional winding method. After the positive / negative electrode sheet is made and baked, the positive / negative electrode sheet is laminated on the separator before winding, and then transported to the winding mechanism. for winding.
[0057] see Figure 5 , Figure 5 It is the winding schematic d...
Embodiment 2
[0069] see Figure 5 , Figure 5 It is the winding schematic diagram of the winding process of the present invention. Such as Figure 5 As shown, the winding device of the present invention includes an unwinding mechanism 100 , a roller passing mechanism 200 , a stacking mechanism 300 and a winding mechanism 400 .
[0070] The unwinding mechanism 100 is used to unwind the positive electrode sheet 1021 , the separator 1031 and the negative electrode sheet 1041 respectively, wherein the positive electrode sheet 1021 , the separator 1031 and the negative electrode sheet 1041 are independently wound on the unwinding mechanism. In this embodiment, the positive electrode sheet 1021, the separator 1031 and the negative electrode sheet 1041 are independently wound on the unwinding mechanism. It does not mean that there is only one layer of separator, but that the separators are alternately arranged on the positive electrode sheet and the negative electrode sheet. Between the negati...
Embodiment 3
[0079] The difference from Embodiments 1 and 2 is that in this embodiment, the upper and lower surfaces of the laminated positive electrode sheet, separator, negative electrode sheet, and separator are covered with PET protective films, respectively. read on Figure 5 , the PET protective film 1011 is wound into a PET protective film roll 101 on the unwinding mechanism 100 . The PET protective film roll 101 , the positive pole roll 102 , the separator roll 103 , the negative pole roll 104 , the separator roll 103 and the PET protective film roll 101 are sequentially arranged on the unwinding mechanism from top to bottom. The PET protective film roll 101 , positive electrode roll 102 , separator roll 103 , negative electrode roll 104 , separator roll 103 and PET protective film roll 101 are unwound simultaneously.
[0080] A pair of pressing rollers 309 and a PET protective film winding mechanism 305 arranged outside the pressing rollers 309 are arranged at the output port of ...
PUM
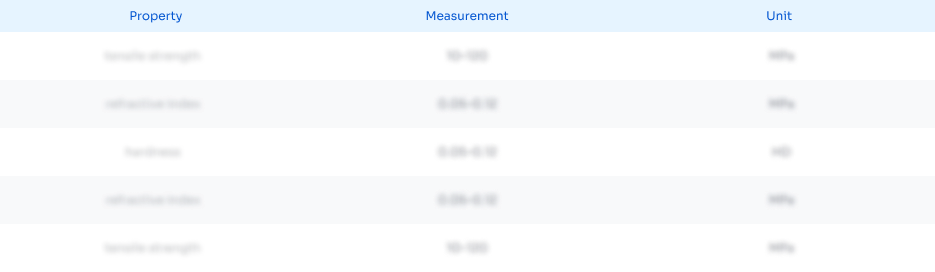
Abstract
Description
Claims
Application Information

- Generate Ideas
- Intellectual Property
- Life Sciences
- Materials
- Tech Scout
- Unparalleled Data Quality
- Higher Quality Content
- 60% Fewer Hallucinations
Browse by: Latest US Patents, China's latest patents, Technical Efficacy Thesaurus, Application Domain, Technology Topic, Popular Technical Reports.
© 2025 PatSnap. All rights reserved.Legal|Privacy policy|Modern Slavery Act Transparency Statement|Sitemap|About US| Contact US: help@patsnap.com