Re-containing zinc alloy for hot-dip galvanizing of low carbon steel with long corrosion-resistant service life
A hot-dip galvanized and corrosion-resistant technology, applied in the field of alloys, can solve the problems of reduced mechanical properties and deterioration of actual performance of materials, and achieves the effect of hindering oxidation and volatilization, and preventing rapid evaporation and oxidation.
- Summary
- Abstract
- Description
- Claims
- Application Information
AI Technical Summary
Problems solved by technology
Method used
Examples
Embodiment 1
[0019] A Re-containing zinc alloy for hot-dip galvanizing of low-carbon steel with excellent corrosion resistance life at 460-600 degrees. In terms of weight percentage, the chemical composition of the material is: Ba: 0.6wt.%, Re: 0.5wt.%, Ge: 0.9wt.%, Cu: 3.2wt.%, Bi: 1.8wt.%, Mo: 0.3 wt.%, the balance is zinc. Preparation method: Add the above-mentioned raw materials into the atmosphere-protected induction furnace, and use a silicon carbide crucible; induction heat to 550 degrees to form an alloy solution, and use the electromagnetic stirring effect to fully stir for about 10 minutes; put the alloy liquid at 550 degrees After heat preservation and standing for 10 minutes, it is cast into the equipment at the same level as the hot top for semi-continuous casting into required round ingots, and the ingot moving speed is 14m / min. The ingot can be used as a zinc alloy for hot-dip galvanizing for anti-corrosion coating treatment of steel; wherein, the working temperature of the...
Embodiment 2
[0022] A Re-containing zinc alloy for hot-dip galvanizing of low-carbon steel with excellent corrosion resistance life at 460-600 degrees. By weight percentage. In terms of weight percentage, the chemical composition of the material is: Ba: 0.7wt.%, Re: 0.4wt.%, Ge: 0.8wt.%, Cu: 3.8wt.%, Bi: 1.6wt.%, Mo: 0.2 wt.%, the balance is zinc. Preparation method: Add the above-mentioned raw materials into the atmosphere-protected induction furnace, and use a silicon carbide crucible; induction heat to 550 degrees to form an alloy solution, and use the electromagnetic stirring effect to fully stir for about 10 minutes; put the alloy liquid at 550 degrees After heat preservation and standing for 10 minutes, it is cast into the equipment at the same level as the hot top for semi-continuous casting into the required round ingot, and the ingot moves down at a speed of 12m / min. The ingot can be used as a zinc alloy for hot-dip galvanizing for anti-corrosion coating treatment of steel; wher...
Embodiment 3
[0025] A Re-containing zinc alloy for hot-dip galvanizing of low-carbon steel with excellent corrosion resistance life at 460-600 degrees. By weight percentage. In terms of weight percentage, the chemical composition of the material is: Ba: 0.6wt.%, Re: 0.5wt.%, Ge: 0.8wt.%, Cu: 3.2wt.%, Bi: 1.9wt.%, Mo: 0.2 wt.%, the balance is zinc. Preparation method: Add the above-mentioned raw materials into the atmosphere-protected induction furnace, and use a silicon carbide crucible; induction heat to 550 degrees to form an alloy solution, and use the electromagnetic stirring effect to fully stir for about 10 minutes; put the alloy liquid at 550 degrees After heat preservation and standing for 10 minutes, it is cast into the equipment at the same level as the hot top for semi-continuous casting into required round ingots, and the ingot moving speed is 16m / min. The ingot can be used as a zinc alloy for hot-dip galvanizing for anti-corrosion coating treatment of steel; wherein, the wor...
PUM
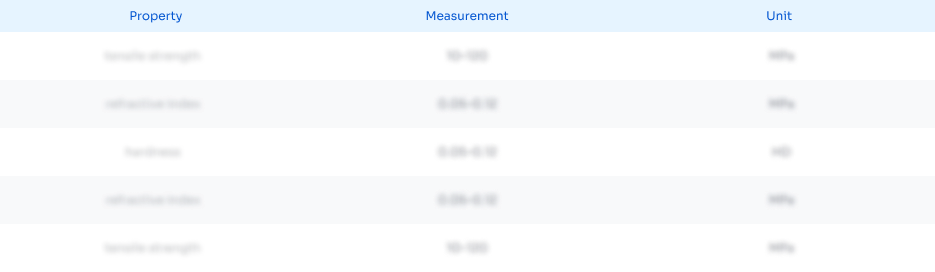
Abstract
Description
Claims
Application Information

- R&D Engineer
- R&D Manager
- IP Professional
- Industry Leading Data Capabilities
- Powerful AI technology
- Patent DNA Extraction
Browse by: Latest US Patents, China's latest patents, Technical Efficacy Thesaurus, Application Domain, Technology Topic.
© 2024 PatSnap. All rights reserved.Legal|Privacy policy|Modern Slavery Act Transparency Statement|Sitemap