Humanoid finger inflatable soft three-finger gripper
A gripper and inflatable technology, which is applied in the field of inflatable soft robot fingers, can solve the problem of low load capacity and achieve the effects of strong impact resistance, large lifting capacity, and strong deformation ability
- Summary
- Abstract
- Description
- Claims
- Application Information
AI Technical Summary
Problems solved by technology
Method used
Image
Examples
specific Embodiment approach 1
[0028] Specific implementation mode one: as Figure 1~5 As shown, the humanoid finger inflatable soft three-finger gripper of this embodiment includes a bottom plate 1, three module bases 2, three soft finger modules 3 and three elastic bandages 4, and each soft finger module 3 includes a soft finger Module body, first air cavity 5, second air cavity 7, first interphalangeal joint trachea 6, second interphalangeal joint trachea 8, restrictive layer 10 and elastic body 9; each soft finger module 3 passes through a module base 2 Installed on one end surface of the bottom plate 1, the body of the soft finger module is provided with a first air chamber 5 and a second air chamber 7 in sequence, the first air chamber 5 communicates with one end of the first interphalangeal joint trachea 6, and the second air chamber 7 communicates with one end of the second interphalangeal joint trachea 8. The back of the soft finger module body is processed with at least two knuckle gap grooves alo...
specific Embodiment approach 2
[0032] Specific implementation mode two: as figure 1 and image 3 As shown, the elastic bandage 4 of the present embodiment is bonded to the finger back and both sides of the soft finger module body. The elastic bandage 4 has a certain degree of elasticity, and the elastic bandage 4 is stretched to a certain extent and no longer stretches. Such a design can limit the expansion volumes of the first air chamber 5 and the second air chamber 7, and continuing to inflate the air chamber after the volume of the air chamber expands to a certain extent will increase the pressure in the air chamber, thereby increasing the driving force of the air chamber. Other components and connections are the same as those in the first embodiment.
specific Embodiment approach 3
[0033] Specific implementation mode three: as figure 2 and Figure 4As shown, the number of knuckle gap grooves in this embodiment is three, the first air cavity 5 is set corresponding to the first knuckle and the second knuckle, and the second air cavity 7 is set corresponding to the third knuckle. With this design, the body of the soft finger module is controlled by two air chambers and two air circuits, in which the first air chamber 5 is used to realize the linkage between the two interphalangeal joints, and the second air chamber 7 is used to realize the independent movement of the metacarpophalangeal joints. The soft humanoid finger is easy to bend at the joint, and the air cavity expands to drive the joint to bend, realizing the human-like finger bending action. Other compositions and connections are the same as those in Embodiment 1 or 2.
PUM
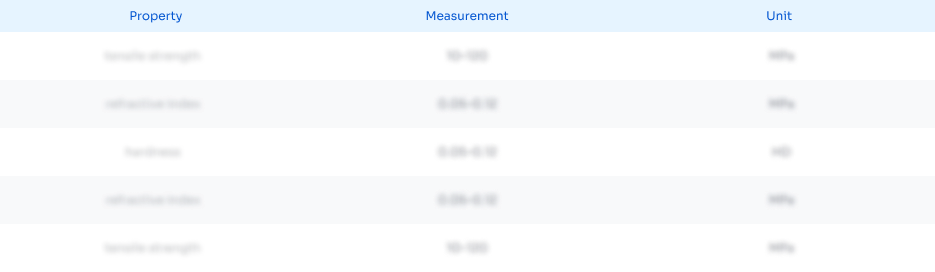
Abstract
Description
Claims
Application Information

- R&D
- Intellectual Property
- Life Sciences
- Materials
- Tech Scout
- Unparalleled Data Quality
- Higher Quality Content
- 60% Fewer Hallucinations
Browse by: Latest US Patents, China's latest patents, Technical Efficacy Thesaurus, Application Domain, Technology Topic, Popular Technical Reports.
© 2025 PatSnap. All rights reserved.Legal|Privacy policy|Modern Slavery Act Transparency Statement|Sitemap|About US| Contact US: help@patsnap.com