Colored stone and fiber concrete artistic board as well as manufacturing method and application thereof
A technology of fiber concrete and colored stone, applied in the field of building decoration materials, can solve the problems of long construction time, poor durability of GRC components, damage to the natural environment, etc., and achieve the effect of high bending strength, high compressive strength and wide sources
- Summary
- Abstract
- Description
- Claims
- Application Information
AI Technical Summary
Problems solved by technology
Method used
Image
Examples
Embodiment 1
[0037] A method for making a colored stone fiber concrete art board, comprising the steps of:
[0038]S1: Mix 1000 parts of colored stones, 825 parts of quartz sand, 355 parts of cement, 4 parts of kaolin, 3.6 parts of water reducing agent, 2 parts of retarder, 0.5 parts of coloring agent and 160 parts of water, and stir to form a surface layer slurry;
[0039] S2: 1000 parts of gravel, 825 parts of medium sand, 5.3 parts of alkali-resistant glass fiber, 355 parts of cement, 4 parts of kaolin, 3.6 parts of water reducer, 2 parts of defoamer, 2 parts of cellulose ether, and 2 parts of retarder 160 parts and 160 parts of water are mixed and stirred to form the base layer slurry;
[0040] S3: The polystyrene board is used to make a model with a ratio of 1:1 to the surface to be decorated. After repeated corrections, the bolts are pre-embedded in place after the mold is turned over with silica gel, and 5mm of surface slurry is sprayed on the surface of the silica gel mold, and it ...
Embodiment 2
[0043] A method for making a colored stone fiber concrete art board, comprising the steps of:
[0044] S1: Mix 977 parts of colored stones, 800 parts of quartz sand, 335 parts of cement, 3 parts of kaolin, 4 parts of water reducing agent, 2 parts of retarder, 0.5 parts of colorant and 154 parts of water, and stir to form a surface layer slurry;
[0045] S2: 977 parts of gravel, 800 parts of medium sand, 5 parts of alkali-resistant glass fiber, 335 parts of cement, 3 parts of kaolin, 4 parts of water reducing agent, 2 parts of defoaming agent, 2 parts of cellulose ether, and 2 parts of retarder 154 parts and 154 parts of water are mixed and stirred to form the base layer slurry;
[0046] S3: The polystyrene board is used to make a model with a ratio of 1:1 to the surface to be decorated. After repeated corrections, the bolts are pre-embedded in place after the mold is turned over with silica gel, and 5mm of surface slurry is sprayed on the surface of the silica gel mold, and it...
Embodiment 3
[0049] A method for making a colored stone fiber concrete art board, comprising the steps of:
[0050] S1: Mix 939 parts of colored stones, 800 parts of quartz sand, 382 parts of cement, 4 parts of kaolin, 3 parts of water reducing agent, 2 parts of retarder, 0.5 parts of colorant and 169 parts of water, and stir to form a surface layer slurry;
[0051] S2: 939 parts of gravel, 800 parts of medium sand, 5.5 parts of alkali-resistant glass fiber, 382 parts of cement, 4 parts of kaolin, 3 parts of water reducer, 2 parts of defoamer, 2 parts of cellulose ether, and 2 parts of retarder After mixing with 169 parts of water, stir to form the base layer slurry;
[0052] S3: The polystyrene board is used to make a model with a ratio of 1:1 to the surface to be decorated. After repeated corrections, the bolts are pre-embedded in place after the mold is turned over with silica gel, and 5mm of surface slurry is sprayed on the surface of the silica gel mold, and it is pressed in place. ,...
PUM
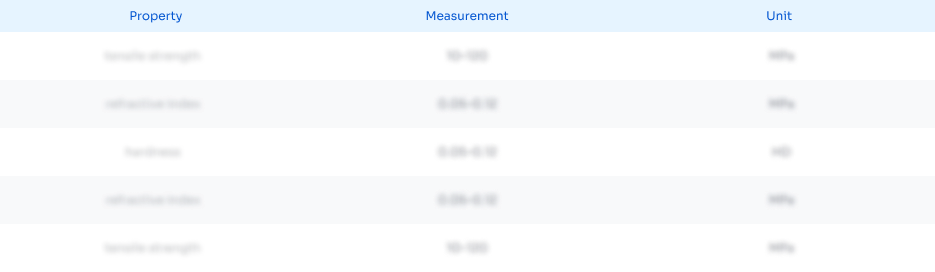
Abstract
Description
Claims
Application Information

- R&D
- Intellectual Property
- Life Sciences
- Materials
- Tech Scout
- Unparalleled Data Quality
- Higher Quality Content
- 60% Fewer Hallucinations
Browse by: Latest US Patents, China's latest patents, Technical Efficacy Thesaurus, Application Domain, Technology Topic, Popular Technical Reports.
© 2025 PatSnap. All rights reserved.Legal|Privacy policy|Modern Slavery Act Transparency Statement|Sitemap|About US| Contact US: help@patsnap.com