Preparation method and application of glucose coated oil-water separation membrane
A technology of oil-water separation membrane and glucose aqueous solution, which is applied in the fields of functional materials and chemical engineering, can solve the problems of high manufacturing cost, complicated production process, difficult production and application, etc., and achieve the effect of slow attenuation, simple operation and large water flow
- Summary
- Abstract
- Description
- Claims
- Application Information
AI Technical Summary
Problems solved by technology
Method used
Image
Examples
Embodiment 1
[0030] (1) Preparation of glucose solution
[0031] Gradually add 0.8g of glucose powder particles into 20mL of deionized water, stir well and leave it for 30min to obtain glucose aqueous solution,
[0032] (2) After adding 37wt% HCl solution to adjust the pH value of the glucose solution obtained in step (1) to 2, a piece of dry qualitative filter paper with a diameter of 70 mm and a pore size of 20-25 μm is put into it and soaked for 2 h,
[0033] (3) Take out the filter paper soaked in the glucose solution in step (2), and then put into 20mL of 50wt% glutaraldehyde aqueous solution and soak for 24h;
[0034] (4) Take out the filter paper soaked in the glutaraldehyde aqueous solution in step (3), wash it with ethanol and deionized water several times to remove the chemical substances remaining on the surface, and dry it in vacuum at 35°C for 24 hours to obtain the glucose-coated oil-water separation membrane.
[0035] The surface morphology and related dimensions of the oi...
Embodiment 2
[0040] (1) Preparation of glucose solution
[0041] Gradually add 14g of glucose powder particles into 20mL of deionized water and stir well, then place it until the solution temperature returns to room temperature to obtain a saturated aqueous solution of glucose,
[0042] (2) After adding 37wt% HCl solution to regulate the pH value of the glucose solution obtained in step (1) to be 2, a piece of dry qualitative filter paper with a diameter of 70 mm and a pore size of 2.5 μm is put into it and soaked for 2 h,
[0043] (3) Take out the filter paper soaked in the glucose solution in step (2), and then put into 20mL of 25wt% glutaraldehyde aqueous solution and soak for 24h;
[0044] (4) Take out the filter paper soaked in the glutaraldehyde aqueous solution in step (3), wash it with ethanol and deionized water several times to remove the chemical substances remaining on the surface, and dry it in vacuum at 35°C for 24 hours to obtain the glucose-coated oil-water separation memb...
Embodiment 3
[0050] (1) Preparation of glucose solution
[0051] Gradually add 2g of glucose powder particles into 20mL of deionized water and leave it for 30min after stirring fully to obtain glucose aqueous solution,
[0052] (2) After adding 37wt% HCl solution to adjust the pH value of the glucose solution obtained in step (1), a piece of dry 50 × 50mm 2 The 300-mesh cotton fiber raw fabric is soaked in it for 4 hours,
[0053] (3) Take out the cotton fiber raw fabric soaked in the glucose solution in the step (2), then put into 20mL of 25wt% glutaraldehyde aqueous solution and soak for 48h;
[0054] (4) Take out the raw cotton fiber fabric soaked in the glutaraldehyde aqueous solution in step (3), wash with ethanol and deionized water several times to remove the chemical substances remaining on the surface, and then vacuum-dry at 35°C for 24 hours to obtain the glucose-coated cloth oil-water separation membrane.
[0055] The surface morphology and related dimensions of the oil-water...
PUM
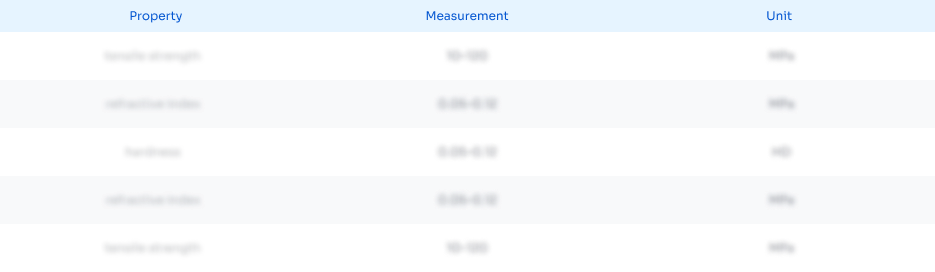
Abstract
Description
Claims
Application Information

- R&D Engineer
- R&D Manager
- IP Professional
- Industry Leading Data Capabilities
- Powerful AI technology
- Patent DNA Extraction
Browse by: Latest US Patents, China's latest patents, Technical Efficacy Thesaurus, Application Domain, Technology Topic, Popular Technical Reports.
© 2024 PatSnap. All rights reserved.Legal|Privacy policy|Modern Slavery Act Transparency Statement|Sitemap|About US| Contact US: help@patsnap.com