Finger joint prosthesis structure
A finger joint and prosthesis technology, applied in the field of finger joint prosthesis structure, can solve the problems of muscle and tendon tissue involvement, failure to reach, dislocation, etc., so as to reduce postoperative complications, reduce the risk of rupture, and achieve reasonable design. Effect
- Summary
- Abstract
- Description
- Claims
- Application Information
AI Technical Summary
Problems solved by technology
Method used
Image
Examples
Embodiment 1
[0039] A finger joint prosthesis structure, including a proximal prosthesis 1, a joint part 2, a distal prosthesis 3, and a rotation shaft 4, and the proximal prosthesis 1 and the joint part 2 form a shaft fit connection through the rotation shaft 4 to achieve flexible joints Rotate to realize that the joint part 2 of the joint is connected with the distal prosthesis 1, the other end of the proximal prosthesis 1 is connected with the proximal expansion screw 5, and the other end of the distal prosthesis 3 is connected with the distal expansion screw 6; the proximal expansion screw 5 and the distal expansion screw 6 are respectively inserted into the medullary cavity at both ends of the joint, and the proximal expansion screw 5 and the distal expansion screw 6 prevent withdrawal.
[0040] The proximal prosthesis 1 comprises a proximal prosthesis joint 7 and a proximal prosthesis handle 8, the joint part 2 comprises a joint part head 9 and a joint part tail 10, and the distal pro...
Embodiment 2
[0042] A finger joint prosthesis structure, including a proximal prosthesis 1, a joint part 2, a distal prosthesis 3, and a rotation shaft 4, and the proximal prosthesis 1 and the joint part 2 form a shaft fit connection through the rotation shaft 4 to achieve flexible joints Rotate to realize that the joint part 2 of the joint is connected with the distal prosthesis 1, the other end of the proximal prosthesis 1 is connected with the proximal expansion screw 5, and the other end of the distal prosthesis 3 is connected with the distal expansion screw 6; the proximal expansion screw 5 and the distal expansion screw 6 are respectively inserted into the medullary cavity at both ends of the joint, and the proximal expansion screw 5 and the distal expansion screw 6 prevent withdrawal.
[0043] The proximal prosthesis 1 comprises a proximal prosthesis joint 7 and a proximal prosthesis handle 8, the joint part 2 comprises a joint part head 9 and a joint part tail 10, and the distal pro...
Embodiment 3
[0049] A finger joint prosthesis structure, including a proximal prosthesis 1, a joint part 2, a distal prosthesis 3, and a rotation shaft 4, and the proximal prosthesis 1 and the joint part 2 form a shaft fit connection through the rotation shaft 4 to achieve flexible joints Rotate to realize that the joint part 2 of the joint is connected with the distal prosthesis 1, the other end of the proximal prosthesis 1 is connected with the proximal expansion screw 5, and the other end of the distal prosthesis 3 is connected with the distal expansion screw 6; the proximal expansion screw 5 and the distal expansion screw 6 are respectively inserted into the medullary cavity at both ends of the joint, and the proximal expansion screw 5 and the distal expansion screw 6 prevent withdrawal.
[0050] The proximal prosthesis 1 comprises a proximal prosthesis joint 7 and a proximal prosthesis handle 8, the joint part 2 comprises a joint part head 9 and a joint part tail 10, and the distal pro...
PUM
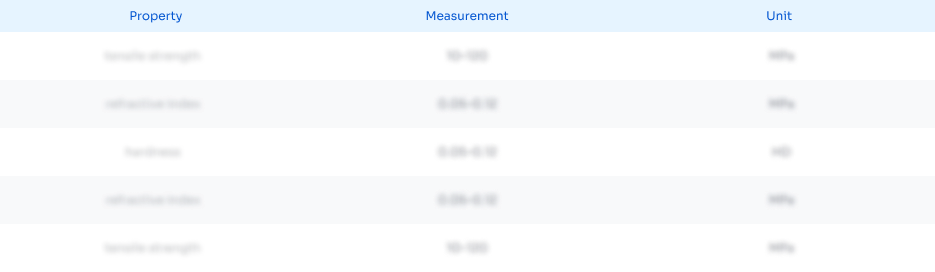
Abstract
Description
Claims
Application Information

- R&D Engineer
- R&D Manager
- IP Professional
- Industry Leading Data Capabilities
- Powerful AI technology
- Patent DNA Extraction
Browse by: Latest US Patents, China's latest patents, Technical Efficacy Thesaurus, Application Domain, Technology Topic, Popular Technical Reports.
© 2024 PatSnap. All rights reserved.Legal|Privacy policy|Modern Slavery Act Transparency Statement|Sitemap|About US| Contact US: help@patsnap.com