Deburring device for stamped chain baffle blade
A deburring and chain technology, applied in grinding/polishing safety devices, metal processing equipment, abrasive belt grinders, etc., can solve problems such as time-consuming and labor-intensive consumption, large consumption of water and abrasives, waste sewage discharge and pollution of the environment, and achieve improvement Utilization rate, man-hour saving, effect of ensuring work quality
- Summary
- Abstract
- Description
- Claims
- Application Information
AI Technical Summary
Problems solved by technology
Method used
Image
Examples
specific Embodiment approach 1
[0018] Specific implementation mode one: combine Figure 1 to Figure 9 To illustrate this embodiment, a deburring device for a stamping chain block described in this embodiment includes a reversing guide rail mechanism, two guide groove plates 1 and two abrasive belt mechanisms, and the two abrasive belt mechanisms are respectively horizontally arranged at different heights. The upper end of each abrasive belt mechanism is fixedly connected with a guide groove plate 1 respectively, and the lower end surface of the guide groove plate 1 is provided with an S-shaped material guide groove 1-1. The discharge end of the material chute 1-1 is connected, and the lower end of the reversing guide rail mechanism is connected with the feed end of the S-shaped material guide chute 1-1 on the lower abrasive belt mechanism. The abrasive belt mechanism includes an abrasive belt 3, a servo motor 4 and two The set of pulleys 2, two sets of pulleys 2 are horizontally arranged side by side, the o...
specific Embodiment approach 2
[0022] Specific implementation mode two: combination Image 6 with Figure 7 To illustrate this embodiment, the abrasive belt mechanism in this embodiment further includes a supporting plate 5 , which is horizontally arranged between two sets of pulleys 2 and supported on the inner side of the upper abrasive belt 3 . Other compositions and connection methods are the same as those in Embodiment 1.
[0023] The supporting plate 5 is designed in this way to support the upper abrasive belt 3, so as to ensure that the abrasive belt 3 carrying the parts remains horizontal, and completes the grinding of the parts.
specific Embodiment approach 3
[0024] Specific implementation mode three: combination Figure 3 to Figure 4 with Figure 6 to Figure 9 This embodiment will be described. The output shaft of the servo motor 4 in this embodiment is connected to the pulley 2 at the discharge end. Other compositions and connection methods are the same as those in the second embodiment.
PUM
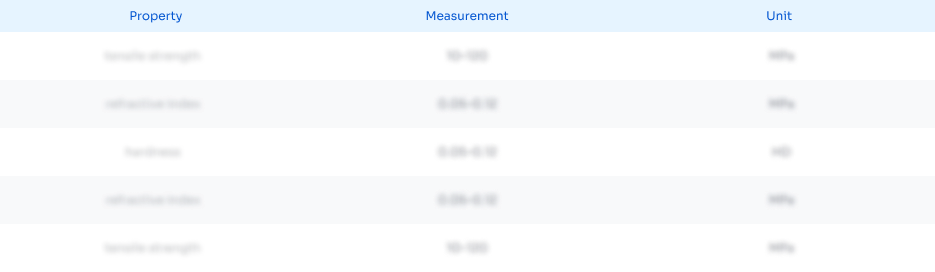
Abstract
Description
Claims
Application Information

- R&D Engineer
- R&D Manager
- IP Professional
- Industry Leading Data Capabilities
- Powerful AI technology
- Patent DNA Extraction
Browse by: Latest US Patents, China's latest patents, Technical Efficacy Thesaurus, Application Domain, Technology Topic, Popular Technical Reports.
© 2024 PatSnap. All rights reserved.Legal|Privacy policy|Modern Slavery Act Transparency Statement|Sitemap|About US| Contact US: help@patsnap.com