Forging forming process of rotating shafts for locomotive
A technology of forging forming and rotating shaft, applied in the field of forging, can solve the problems of mechanical properties, microstructure that cannot meet the conditions of use, long processing time of forgings, low material utilization rate, etc. cost effect
- Summary
- Abstract
- Description
- Claims
- Application Information
AI Technical Summary
Problems solved by technology
Method used
Image
Examples
Embodiment Construction
[0038] The embodiments of the present invention will be described in detail below with reference to the accompanying drawings, but the present invention can be implemented in many different ways defined and covered by the claims.
[0039] A forging forming process for a rotating shaft for a locomotive, comprising the following steps:
[0040] a. Blanking: select the raw material based on the appropriate specifications of the elongated length of the small-diameter rod and the upsetting height-to-diameter ratio of the large-diameter end.
[0041] The selection method of the specification of the raw material: the weight of the disc on the upper part of the rod M×(1+fire consumption coefficient)=the mass m of the raw material required at the large diameter end; then calculate the diameter specification of the raw material according to the required weight m of the raw material. The maximum allowable aspect ratio here is 5, that is, L / D≤5; according to m=ρ×V, because the raw materia...
PUM
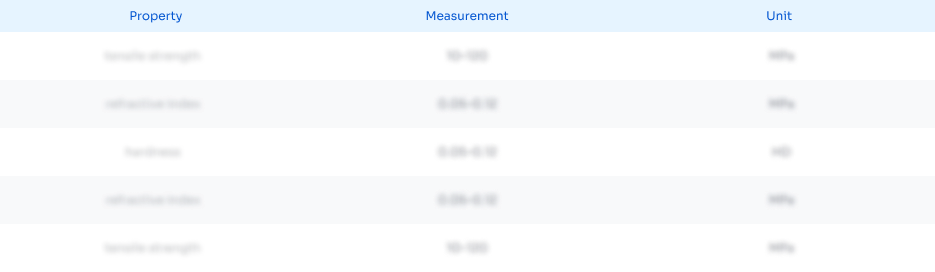
Abstract
Description
Claims
Application Information

- R&D
- Intellectual Property
- Life Sciences
- Materials
- Tech Scout
- Unparalleled Data Quality
- Higher Quality Content
- 60% Fewer Hallucinations
Browse by: Latest US Patents, China's latest patents, Technical Efficacy Thesaurus, Application Domain, Technology Topic, Popular Technical Reports.
© 2025 PatSnap. All rights reserved.Legal|Privacy policy|Modern Slavery Act Transparency Statement|Sitemap|About US| Contact US: help@patsnap.com