Lithium battery defect detection system and method based on machine vision
A defect detection and machine vision technology, applied in the direction of optical testing defects/defects, instruments, measuring devices, etc., can solve the problems of non-real-time detection, artificial naked eye detection, low detection efficiency, etc., to improve detection accuracy and stability, save money Human resources, the effect of high detection efficiency
- Summary
- Abstract
- Description
- Claims
- Application Information
AI Technical Summary
Problems solved by technology
Method used
Image
Examples
Embodiment Construction
[0041] The present invention will be further described below in conjunction with specific drawings and embodiments.
[0042] Lithium battery defect detection system based on machine vision, such as figure 1 As shown, it includes a CCD camera 1, a visual detection system 2, and a control system 3; wherein the visual detection system 2 can be a computer on which visual detection software is installed; the control system 3 can be an industrial computer; the detection station 4 can be set A sensor to detect whether there is a lithium battery in the fixture, and if so, trigger the CCD camera 1 to collect images accordingly;
[0043] The CCD camera 1 is aligned laterally at the detection station 4 to take images of the side of the lithium battery; the CCD camera 1 is connected to the visual inspection system 2, and the visual inspection system 2 is connected to the control system 3;
[0044] figure 2 shows the normal situation after the trimming process of the lithium battery, th...
PUM
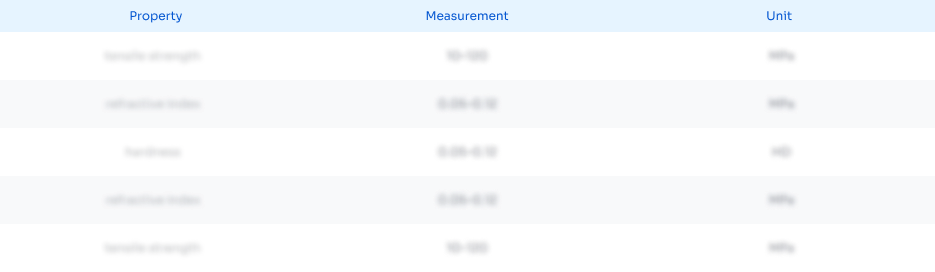
Abstract
Description
Claims
Application Information

- R&D
- Intellectual Property
- Life Sciences
- Materials
- Tech Scout
- Unparalleled Data Quality
- Higher Quality Content
- 60% Fewer Hallucinations
Browse by: Latest US Patents, China's latest patents, Technical Efficacy Thesaurus, Application Domain, Technology Topic, Popular Technical Reports.
© 2025 PatSnap. All rights reserved.Legal|Privacy policy|Modern Slavery Act Transparency Statement|Sitemap|About US| Contact US: help@patsnap.com