A production process of aluminized laser paper
A production process, laser paper technology, applied in metal material coating process, wrapping paper, wrapping paper, etc., can solve the lack of durability, compression resistance, solvent resistance, unclear edge of aluminum plating pattern, product quality impact, etc. problems, to achieve the effect of solving unclear edges, high yield, and improving efficiency
- Summary
- Abstract
- Description
- Claims
- Application Information
AI Technical Summary
Problems solved by technology
Method used
Examples
Embodiment 1
[0026] Embodiment 1: a kind of production technology of aluminized laser paper, comprises the following steps:
[0027] 1) Coating the release agent on the substrate to form a release layer;
[0028] 2) Dry the substrate coated with the release material;
[0029] 3) Emboss the dried film to make the surface of the substrate have a laser pattern;
[0030] 4) Then carry out vacuum aluminum plating on the base material, the vacuum degree is 5*10 -2 , and then apply a protective layer to the specified position;
[0031] 5) Immerse the substrate coated with the protective layer in an alkaline liquid pool to wash aluminum, the alkaline liquid used is barium hydroxide solution, and dry it again;
[0032] 6) Apply glue on the surface of the substrate at fixed points, then use compound equipment to compound the substrate and base paper, and then dry it again;
[0033] 7) The composite paper is matured, the base material is peeled off on the running equipment, and the laser pattern ...
Embodiment 2
[0036] Embodiment 2: a kind of production technology of aluminized laser paper, comprises the following steps:
[0037] 1) Coating the release agent on the substrate to form a release layer;
[0038] 2) Dry the substrate coated with the release material;
[0039] 3) Emboss the dried film to make the surface of the substrate have a laser pattern;
[0040] 4) Then carry out vacuum aluminum plating on the base material, the vacuum degree is 7*10 -2 Pa, followed by protective layer coating on the specified position;
[0041] 5) Immerse the substrate coated with the protective layer in an alkaline liquid pool to wash aluminum, the alkaline liquid used is barium hydroxide solution, and dry it again;
[0042] 6) Apply glue on the surface of the substrate at fixed points, then use compound equipment to compound the substrate and base paper, and then dry it again;
[0043] 7) The composite paper is matured, the base material is peeled off on the running equipment, and the laser pa...
PUM
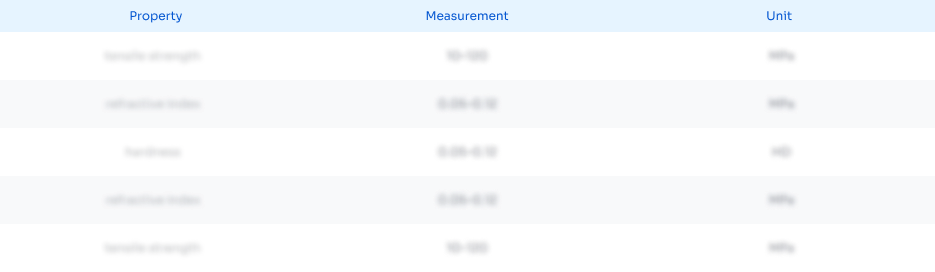
Abstract
Description
Claims
Application Information

- Generate Ideas
- Intellectual Property
- Life Sciences
- Materials
- Tech Scout
- Unparalleled Data Quality
- Higher Quality Content
- 60% Fewer Hallucinations
Browse by: Latest US Patents, China's latest patents, Technical Efficacy Thesaurus, Application Domain, Technology Topic, Popular Technical Reports.
© 2025 PatSnap. All rights reserved.Legal|Privacy policy|Modern Slavery Act Transparency Statement|Sitemap|About US| Contact US: help@patsnap.com