Active flexible telescopic truss structure
A truss structure and truss technology, applied in the field of variant aircraft structure design, can solve problems such as limited driving capacity, single fixed deformation form, and heavy structure weight.
- Summary
- Abstract
- Description
- Claims
- Application Information
AI Technical Summary
Problems solved by technology
Method used
Image
Examples
Embodiment Construction
[0029] In order to make the objectives, technical solutions and advantages of the present invention clearer, the technical solutions in the embodiments of the present invention will be described in more detail below in conjunction with the drawings in the embodiments of the present invention.
[0030] like figure 1 The active flexible stretchable truss structure shown includes an upper panel 1 , a lower panel 2 , a telescopic truss 3 , a spring 4 and a controllable alloy wire 5 .
[0031] The upper panel 1 and the lower panel 2 are arranged opposite to each other. It should be noted that although the upper and lower panels shown in the figure are regular planes and arranged in parallel, the upper panel 1 and the lower panel 2 can be metal plates with some curvature, and the upper panel 1 and the lower panel 2 can be non- parallel state, but it is necessary to ensure that the telescopic truss 3 can be arranged between the upper panel 1 and the lower panel 2, and that the teles...
PUM
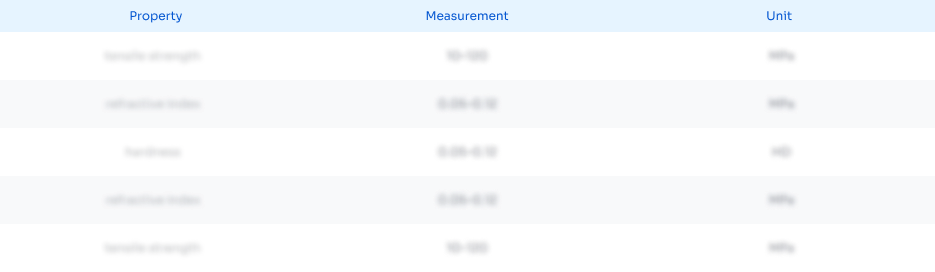
Abstract
Description
Claims
Application Information

- R&D
- Intellectual Property
- Life Sciences
- Materials
- Tech Scout
- Unparalleled Data Quality
- Higher Quality Content
- 60% Fewer Hallucinations
Browse by: Latest US Patents, China's latest patents, Technical Efficacy Thesaurus, Application Domain, Technology Topic, Popular Technical Reports.
© 2025 PatSnap. All rights reserved.Legal|Privacy policy|Modern Slavery Act Transparency Statement|Sitemap|About US| Contact US: help@patsnap.com