System and method for optical coupling image acquisition time calibration
An image acquisition and optical coupling technology, applied in the field of image acquisition, can solve the problems of influence, the light source cannot be installed, and cannot work normally, and achieves the effects of high measurement accuracy, no damage to measurement, and avoidance of dislocation
- Summary
- Abstract
- Description
- Claims
- Application Information
AI Technical Summary
Problems solved by technology
Method used
Image
Examples
Embodiment 1
[0072] figure 1 It is a system diagram of the optical coupling image acquisition time calibration in Embodiment 1 of the present invention. See figure 1 , the system consists of:
[0073] The system time master control module 1 is respectively coupled with the logic control module 2 and the trigger module 3 to provide a reference time for the logic control module 2 and the trigger module 3 .
[0074] The logic control module 2 receives a reference time, and generates an electrical parameter control signal and a period control signal based on the reference time.
[0075] The temporal light generation module 3 includes a light source matrix sub-module 402 and an electrical parameter sub-module 401, the light source matrix sub-module 402 and the electrical parameter sub-module 401 are coupled, wherein the light source matrix sub-module 401 includes at least one light emitting unit.
[0076] The electrical parameter sub-module 401 is coupled with the logic control module 2, rec...
Embodiment 2
[0101] Utilizing the optical coupling type image acquisition time calibration system provided by the present invention, this embodiment provides an optical coupling type image acquisition time calibration method, Figure 4 For the flow chart of the method for calibrating the time of optically coupled image acquisition in Embodiment 2 of the present invention, please refer to Figure 4 , the method includes:
[0102] Step S101: system installation and setting steps: including:
[0103] According to the test requirements, set the relative position of the object under test and the camera, couple the system time master control module with the logic control module and the trigger module respectively, couple the quick search trigger module with the camera, and connect the camera with the image sensor Coupling, coupling the image sensor with the image processing module;
[0104] The logic control module is coupled with the time light generation module, the time light generation mod...
Embodiment 3
[0129] Using the optically coupled image acquisition time calibration system provided by the present invention, and on the basis of the optically coupled image acquisition time calibration method provided by the present invention, this embodiment provides a method for accurately measuring the distance between two or more cameras. The time difference method between startups, Figure 5 For the flow chart of precise positioning camera startup time difference in Embodiment 3 of the present invention, please refer to Figure 5 , the method includes:
[0130] Step S201: System installation steps
[0131] According to the test requirements, set the relative position of the object under test and the camera, couple the system time master control module with the logic control module and the trigger module respectively, couple the quick search trigger module with the camera, and connect the camera with the image sensor Coupling, the image sensor is coupled with the image processing mod...
PUM
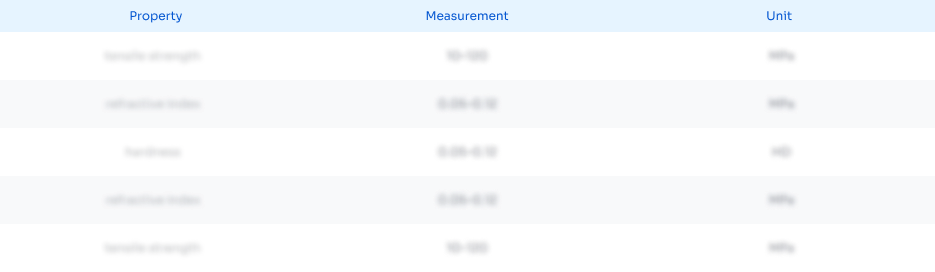
Abstract
Description
Claims
Application Information

- R&D Engineer
- R&D Manager
- IP Professional
- Industry Leading Data Capabilities
- Powerful AI technology
- Patent DNA Extraction
Browse by: Latest US Patents, China's latest patents, Technical Efficacy Thesaurus, Application Domain, Technology Topic, Popular Technical Reports.
© 2024 PatSnap. All rights reserved.Legal|Privacy policy|Modern Slavery Act Transparency Statement|Sitemap|About US| Contact US: help@patsnap.com