Adsorptive desulfurization technology for liquefied petroleum gas
A liquefied petroleum gas and adsorption desulfurization technology, which is applied in the petroleum industry, gas fuel, gas treatment, etc., can solve the problems of low sulfur in adsorption desulfurizers, large differences in process conditions, unfavorable popularization and application, etc., and achieve the improvement of adsorption sulfur capacity, adsorption Sulfur capacity improvement and enhanced chemical adsorption effect
- Summary
- Abstract
- Description
- Claims
- Application Information
AI Technical Summary
Problems solved by technology
Method used
Image
Examples
Embodiment 1
[0029] Preparation of adsorbent
[0030] Adsorbent A
[0031] Take Al 2 O 3 50g, add 60g of distilled water, 8g of concentrated nitric acid and mix well, take 100g of 13X molecular sieve and 3g of sesbania powder into the above mixture, extrude it, dry at 110℃ for 4 hours, calcined at 550℃ for 5 hours, make Into the catalyst carrier. Take 15g of ammonium metatungstate and 3g of nickel nitrate to dissolve in distilled water to make 200g of solution. The carrier was immersed in the solution and shaken. After about 6 hours, the carrier was filtered out, dried at 110°C for 6 hours, and then calcined at 550°C for 5 hours. The adsorbent A loaded with tungsten and nickel was prepared.
[0032] Adsorbent B
[0033] Take Al 2 O 3 20g, add 30g of distilled water, 8g of concentrated nitric acid and mix well, take 100g of Y-type molecular sieve, add 3g of sesame powder to the above mixture, extrude it, dry at 110℃ for 4 hours, calcined at 550℃ for 5 hours, make Into the catalyst carrier. Tak...
Embodiment 2
[0037] Preparation of adsorbent
[0038] Adsorbent A
[0039] Take Al 2 O 3 20g, add 50g of distilled water, 8g of concentrated nitric acid and mix evenly, take 100g of 13X molecular sieve, add 3g of sesame powder to the above mixture, extrude, dry at 110°C for 4 hours, and calcined at 550°C for 5 hours to make Catalyst carrier. Take 15g of ammonium metatungstate, 5g of nickel nitrate and 1g of cerium nitrate to dissolve with distilled water to make 200g of solution. The carrier was immersed in the solution and shaken. After about 6 hours, the carrier was filtered out, dried at 110°C for 6 hours, and then calcined at 550°C for 5 hours. The adsorbent A loaded with tungsten, nickel and cerium was prepared.
[0040] Adsorbent B
[0041] Take Al 2 O 3 60g, add 60g of distilled water, 8g of concentrated nitric acid and mix well, take 100g of Y-type molecular sieve, add 3g of sesame powder to the above mixture, extrude it, dry at 110°C for 4 hours, and calcinate at 550°C for 5 hours. In...
Embodiment 3
[0045] Preparation of adsorbent
[0046] Adsorbent A
[0047] Take Al 2 O 3 30g, add 50g of distilled water, 8g of concentrated nitric acid and mix well, take 100g of type A molecular sieve, add 3g of sesame powder to the above mixture, extrude, dry at 110°C for 4 hours, and calcinate at 550°C for 5 hours. Into the catalyst carrier. Dissolve 20 g of ammonium metatungstate, 6 g of nickel nitrate and 5 g of cerium nitrate in distilled water to prepare a 200 g solution. The carrier was immersed in the solution and shaken. After about 6 hours, the carrier was filtered out, dried at 110°C for 6 hours, and then calcined at 550°C for 5 hours. The adsorbent A loaded with tungsten, nickel and cerium was prepared.
[0048] Adsorbent B
[0049] Take Al 2 O 3 60g, add 60g distilled water, 8g concentrated nitric acid and mix well, take 100g β-molecular sieve and 3g sesbania powder into the above mixture, extrude it, dry at 110℃ for 4 hours, and calcined at 550℃ for 5 hours. Into the catalyst c...
PUM
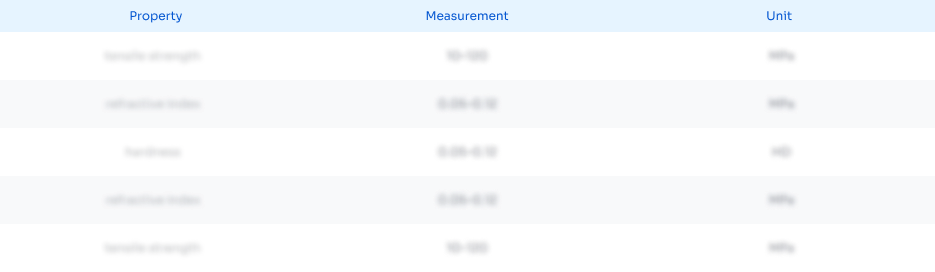
Abstract
Description
Claims
Application Information

- Generate Ideas
- Intellectual Property
- Life Sciences
- Materials
- Tech Scout
- Unparalleled Data Quality
- Higher Quality Content
- 60% Fewer Hallucinations
Browse by: Latest US Patents, China's latest patents, Technical Efficacy Thesaurus, Application Domain, Technology Topic, Popular Technical Reports.
© 2025 PatSnap. All rights reserved.Legal|Privacy policy|Modern Slavery Act Transparency Statement|Sitemap|About US| Contact US: help@patsnap.com