Robot grinding and polishing system for medical artificial limbs
A technology of robots and prosthetics, applied in the field of automatic assembly equipment for medical prosthetics, which can solve problems such as inconsistent sizes and damage to the cardiopulmonary system of workers
- Summary
- Abstract
- Description
- Claims
- Application Information
AI Technical Summary
Problems solved by technology
Method used
Image
Examples
Embodiment Construction
[0038] The present invention will be further described in detail below in conjunction with the accompanying drawings, but does not constitute any limitation to the present invention. Similar component numbers in the accompanying drawings represent similar components. As mentioned above, the present invention provides a robot grinding and polishing system for medical prostheses. In the high-precision manufacturing process of titanium alloy brackets, the automatic feeding of titanium alloy brackets is realized by using the workbench, and the automatic feeding of titanium alloy brackets is realized by industrial robots. Automatic clamping, two sets of polishing mechanisms are used to realize the polishing operation of the titanium alloy bracket, and the conveyor belt automatically outputs after polishing; the robot grinding and polishing system of the medical prosthesis of the present invention realizes the fully automatic unmanned polishing of the titanium alloy bracket Operation...
PUM
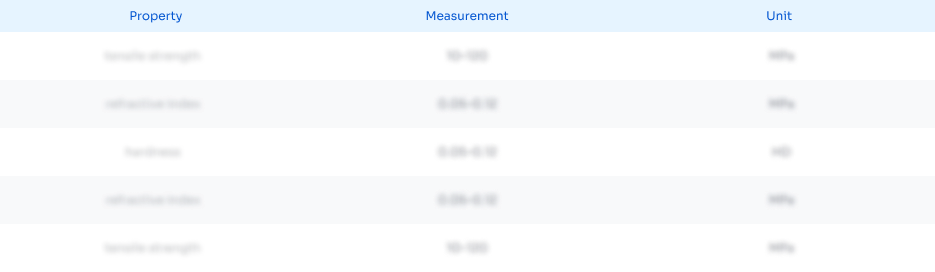
Abstract
Description
Claims
Application Information

- R&D
- Intellectual Property
- Life Sciences
- Materials
- Tech Scout
- Unparalleled Data Quality
- Higher Quality Content
- 60% Fewer Hallucinations
Browse by: Latest US Patents, China's latest patents, Technical Efficacy Thesaurus, Application Domain, Technology Topic, Popular Technical Reports.
© 2025 PatSnap. All rights reserved.Legal|Privacy policy|Modern Slavery Act Transparency Statement|Sitemap|About US| Contact US: help@patsnap.com